In modern industries, pressure vessels are essential equipment widely used in chemical, energy, food, and pharmaceutical sectors. The quality of their design mainly depends on the accuracy of wall thickness calculations. However, ensuring that the thickness meets safety requirements while balancing cost and performance is always a key concern for both buyers and manufacturers. Pressure vessel wall thickness calculation becomes even more critical in complex conditions like high pressure, high temperature, or corrosive media.
When customizing pressure vessels, customers often want to know how to determine the right wall thickness. It needs to meet operational demands but avoid unnecessary costs caused by overdesign. Wall thickness depends on several factors, such as design pressure, temperature, material properties, and corrosion allowance. Each factor requires careful consideration.
Next, we will explain the theoretical formulas for calculating wall thickness and show a complete design process with a real-world example. We will also share tips on optimizing wall thickness for different materials and working conditions, along with practical advice to avoid common mistakes.
Theoretical Basis for Pressure Vessel Wall Thickness Calculation
Wall Thickness Formula for Cylindrical Pressure Vessels
For cylindrical pressure vessels under internal pressure, the wall thickness can be calculated using the following formula:
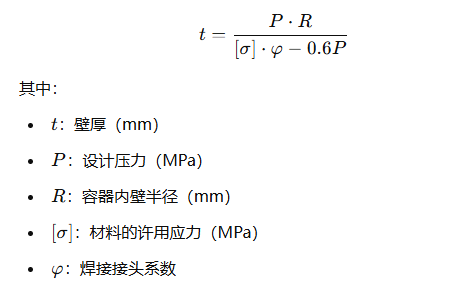
Wall Thickness Formula for Spherical Pressure Vessels
For spherical pressure vessels, the wall thickness formula is slightly different:
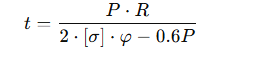
Note: The allowable stress [σ] in the formulas needs adjustment based on the material’s performance at the operating temperature. Also, the welding joint efficiency φ depends on the quality level of the welding process.
How Do Key Factors Affect Pressure Vessel Wall Thickness Calculation?
The core of wall thickness calculation lies in accurately evaluating each variable in the formula. Below is a detailed analysis of several key factors:
Design Pressure and Design Temperature
- Design Pressure: This is the maximum pressure a pressure vessel might endure during operation. It is usually 1.1 to 1.3 times the working pressure.
- Design Temperature: This directly affects the material’s allowable stress. At high temperatures, material strength decreases, so the allowable stress must be adjusted accordingly.
Allowable Stress of the Material
The allowable stress is a crucial parameter for pressure vessel materials. It depends on the material’s yield strength, tensile strength, and design temperature. Common materials like carbon steel, stainless steel, and alloy steel have their allowable stress values clearly defined in relevant standards.
Corrosion Allowance
To extend the service life of the equipment, it is necessary to add a corrosion allowance (C) when calculating wall thickness:
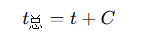
The value of C depends on the corrosiveness of the medium and the design life of the equipment. It is typically set between 2 to 3 mm.
Manufacturing Tolerances and Additional Factors
Thickness deviations during manufacturing and the impact of welding processes can affect wall thickness. To account for these, standards usually specify additional factors to ensure sufficient design margin.
Wall Thickness Calculation Process in Practice (With Case Study)
The following is a step-by-step simulation of wall thickness calculation for a pressure vessel. It uses specific parameters to help you clearly understand each operation and its significance.
Case Background
A chemical company needs to design a cylindrical pressure vessel to handle internal pressure. The known parameters are:
- Design Pressure (P): 2.5 MPa
- Design Temperature: 200°C
- Internal Diameter (D): 2000 mm
- Material Used: Q345R (carbon steel, allowable stress [σ] at design temperature: 150 MPa)
- Welding Joint Efficiency (φ): 0.85 (third-grade welding quality)
- Corrosion Allowance (C): 3 mm
- Manufacturing Thickness Deviation: 2 mm
Steps and Calculations
Step 1: Define Working Conditions and Design Parameters
Gather all known data, including design pressure, design temperature, medium characteristics, vessel dimensions, and material properties.
Step 2: Choose Applicable Standards and Materials
Select the GB/T 150 “Safety Technical Code for Pressure Vessels” as the design standard. Use Q345R as the material, with an allowable stress of 150 MPa at 200°C. Set the welding joint efficiency to 0.85.
Step 3: Substitute Values into the Formula to Calculate Theoretical Wall Thickness
Use the formula for calculating the wall thickness of a cylindrical pressure vessel under internal pressure:
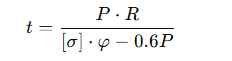
Calculate the theoretical wall thickness as follows:
First, determine the internal radius of the vessel:
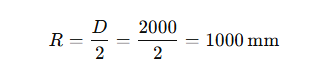
Substitute into the formula:
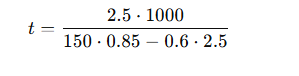
Calculate:
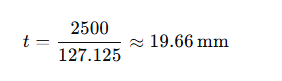
The theoretical wall thickness is 19.66 mm.
Step 4: Adjust for Corrosion Allowance and Manufacturing Deviation
Use the formula to calculate the total wall thickness adjustment:
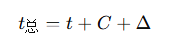
Where:
- Corrosion Allowance (C): 3 mm
- Manufacturing Thickness Deviation (Δ): 2 mm
Calculate:

The final designed wall thickness is 24.66 mm.
Step 5: Verify Feasibility of Wall Thickness
- Machining Verification: Check if the wall thickness meets manufacturing requirements. For example, if the vessel requires welding, the wall thickness must not be less than the minimum specified in the standards, usually 6 mm. A thickness of 24.66 mm is well above the minimum, so it meets the requirement.
- Material Strength Verification: Confirm that Q345R can maintain sufficient strength at 200°C. Ensure the wall thickness prevents plastic deformation or fatigue failure due to temperature changes.
- Operational Safety Verification: Assess whether the wall thickness is adequate for long-term use, especially in corrosive environments. The chosen thickness provides enough margin to support a service life of 10-20 years.
Results and Optimization Suggestions
The final calculated wall thickness is 24.66 mm. For actual manufacturing, using a standard plate thickness of 25 mm is recommended. This simplifies procurement and fabrication while adding an extra 1% safety margin.
Key Considerations
- Recalculate the wall thickness if there are changes in design pressure or temperature.
- Adjust the corrosion allowance based on the medium. For highly corrosive media, increase the allowance to 5 mm or more.
- For high-pressure equipment, strictly control welding quality and aim to maximize the welding joint efficiency (φ).
This calculation process allows you to adjust the wall thickness design precisely based on actual requirements. It helps ensure safety while optimizing costs.
How to Avoid Common Mistakes
- Underestimating Corrosion Allowance
Some designers ignore the long-term corrosiveness of the medium, which can lead to premature failure of the equipment. The solution is to reasonably increase the corrosion allowance and choose corrosion-resistant materials. - Overlooking the Effect of Welding Quality on Wall Thickness
The welding joint efficiency (φ) is usually less than 1. Ignoring this factor can result in insufficient wall thickness. Designers need to carefully select the appropriate coefficient based on welding quality. - Overdesign Leading to Higher Costs
Excessive design pressure and temperature can cause overly thick walls, which increases manufacturing costs. It is better to set design parameters reasonably and avoid unnecessary expenses.
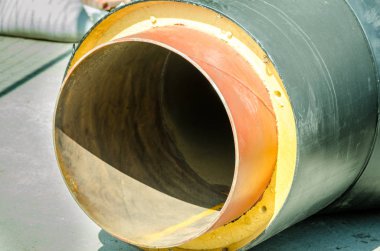
Differences in Wall Thickness for Different Materials
Allowable Stress Differences
- Carbon Steel (e.g., Q235, Q345R):
Carbon steel has relatively low allowable stress at room temperature (about 150 MPa) and performs poorly at high temperatures. Under high-pressure conditions, increasing the wall thickness is often necessary to ensure strength. It is suitable for vessels in medium and low-pressure conditions. - Stainless Steel (e.g., 304, 316L):
Stainless steel has higher allowable stress (above 200 MPa), better strength, and greater toughness compared to carbon steel. Its strong corrosion resistance allows thinner walls for the same pressure. For example, 316L is widely used in corrosive environments due to its excellent resistance to pitting corrosion. - Duplex Stainless Steel (e.g., 2205, 2507):
Duplex stainless steel has an allowable stress about 50% higher than austenitic stainless steel. It combines high strength with excellent corrosion resistance. In high-pressure or highly corrosive environments, the wall thickness can be reduced by 30% or more compared to carbon steel.
Temperature Performance Differences
- Carbon Steel:
Carbon steel performs well from room temperature to 350°C. However, when temperatures exceed 400°C, its strength drops significantly, so the wall thickness must increase to compensate. - Stainless Steel and Duplex Stainless Steel:
Stainless steel has better high-temperature performance than carbon steel. Grades 304 and 316L maintain good strength below 500°C. Duplex stainless steel performs best at 250–300°C, but it may experience phase separation at higher temperatures, so careful evaluation is necessary. - Nickel-Based Alloys (e.g., Inconel, Hastelloy):
Nickel-based alloys have exceptional temperature resistance, withstanding temperatures above 700°C while maintaining strength. In extreme high-temperature applications, wall thickness can be significantly reduced.
Corrosion Resistance Differences
- Carbon Steel:
Carbon steel has poor corrosion resistance, so it usually requires a corrosion allowance of 2–6 mm. This directly increases wall thickness. Using linings, such as anti-corrosion coatings, can help reduce the corrosion allowance. - Stainless Steel:
Stainless steel naturally resists corrosion in weak acids and bases, often eliminating the need for a corrosion allowance. However, in highly corrosive media like hydrochloric acid or chlorine gas, some allowance may still be necessary. - Nickel-Based Alloys and Titanium Alloys:
Nickel-based alloys have outstanding corrosion resistance, especially in strong oxidizing or reducing media. They often require little or no corrosion allowance, resulting in thinner walls. However, their material cost is very high.
Processing and Manufacturing Characteristics
Processing characteristics also impact wall thickness:
- Carbon Steel:
Carbon steel is easy to weld and process. Even with thicker walls, the cost impact is limited. - Stainless Steel and Duplex Steel:
These materials require higher welding quality, and thinner walls demand better welding stability. - Nickel-Based Alloys and Titanium Alloys:
These materials are difficult to process, and thin-wall structures require extra reinforcement. Automated cutting and precise machining are often necessary.
Welding Joint Efficiency (φ) Impact
Welding quality directly affects wall thickness design. High-strength materials like duplex steel usually have higher welding joint efficiency (close to 1), giving them an advantage in thickness calculation. In contrast, carbon steel vessels with lower welding quality coefficients (0.85–0.9) often require additional thickness to compensate for strength limitations.
Summary of Wall Thickness Differences and Comparisons
Material Type | Allowable Stress (MPa) | Corrosion Allowance | Temperature Range (°C) | Wall Thickness Characteristics | Suitable Applications |
Carbon Steel | 120–150 | 2–6 mm | -20 to 400 | Relatively thick, moderate | Medium to low pressure, non-corrosive environments |
Stainless Steel | 200–240 | None–3 mm | -60 to 500 | Thinner walls, strong corrosion resistance | Corrosive media or high-temperature environments |
Duplex Stainless Steel | 300–350 | None–3 mm | -50 to 300 | Thinnest walls, highest strength | High pressure, highly corrosive environments |
Nickel-Based Alloys | 240–400 | None–2 mm | -100 to 700 | Extremely thin walls, ideal for extreme conditions | Highly corrosive, high-temperature, or high-pressure environments |
Aluminum Alloys | 80–120 | 2–5 mm | -100 to 150 | Thicker walls, suitable for lightweight designs | Low pressure, low temperature, food and pharmaceutical industries |
The Impact of Wall Thickness on Product Quality
Wall thickness is a key factor in the design of pressure vessels. It has a significant impact on the quality and performance of the equipment. The wall thickness directly affects the strength, safety, and service life of the vessel.
- Pressure Resistance:
Wall thickness determines the vessel’s ability to handle working pressure and withstand impact loads. Thicker walls provide greater strength and better resistance to internal pressure failure. This is especially important for high-pressure operations, as it helps prevent deformation or rupture. - Corrosion Resistance:
In corrosive environments, increasing the wall thickness provides additional corrosion allowance. This extends the service life of the vessel. In industries like chemical and pharmaceutical manufacturing, a well-designed wall thickness is an effective way to combat medium-induced corrosion. - Durability and Stability:
Thicker walls can significantly improve the vessel’s fatigue life. This is particularly beneficial in conditions involving high temperature, high pressure, or frequent start-stop cycles. Thicker walls help resist the accumulation of thermal and mechanical stresses. - Safety:
Adequate wall thickness ensures that the pressure vessel meets national standards and industry regulations, such as ASME and GB150. This helps prevent safety hazards caused by design or manufacturing deficiencies.
How Do We Provide Professional Support? Why Choose Minnuo?
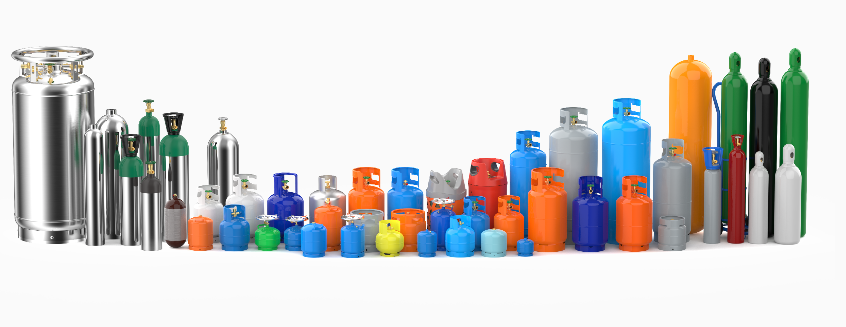
- Outstanding Pressure Resistance:
MinNuo strictly follows national and international design standards, such as GB150 and ASME BPVC. During the design phase, we use precise finite element analysis and pressure testing to ensure that the wall thickness meets or even exceeds working pressure requirements. For high-pressure scenarios, we conduct multiple simulations and experimental verifications. Our products not only meet standard requirements but also include sufficient safety margins. This ensures our pressure vessels operate reliably and stably, even under high-pressure conditions. - Reliable Corrosion Resistance:
To handle corrosive media, we do more than rely on corrosion allowance in the wall thickness. We also enhance performance through material selection and process optimization. MinNuo uses highly corrosion-resistant stainless steel and alloy materials, combined with advanced internal protective coating technologies. Our designs always exceed industry corrosion allowance standards by 1–3 mm, ensuring long-term durability and protection for the vessels. - Durability and Stability:
MinNuo continuously optimizes wall thickness to ensure the vessels withstand high temperature, high pressure, and thermal cycling loads. We use advanced welding and heat treatment technologies to maximize the mechanical performance of the walls, preventing fatigue failures caused by temperature fluctuations. Before delivery, all products undergo rigorous simulated working condition tests, including high-temperature stress tests and cyclic pressure tests, to guarantee their durability in extreme environments. - Commitment to Safety:
MinNuo places customer safety as the highest priority. Every pressure vessel undergoes pressure testing that exceeds standard requirements, ensuring wall thickness far surpasses actual operational needs. During production, we use laser thickness measurement technology to monitor critical areas in real time, ensuring uniform wall thickness and eliminating risks from weak spots. Additionally, each product comes with a detailed design calculation sheet and inspection report. With full transparency in every process, customers can trust our products completely.
Frequently Asked Questions
About Parameter Determination
- How to Determine Corrosion Allowance?
Corrosion allowance depends on the corrosiveness of the medium, the equipment’s design life, and the anti-corrosion measures in place:
- For weakly corrosive media, set C = 1–2 mm.
- For moderately corrosive media, set C = 2–4 mm.
- For highly corrosive media, set C = 5–6 mm or use corrosion-resistant materials.
The longer the equipment’s service life, the greater the corrosion allowance should be. If anti-corrosion coatings or cathodic protection are applied, the corrosion allowance can be appropriately reduced.
- Why Consider Manufacturing Deviations?
Manufacturing deviations compensate for errors during processing and material production to ensure the actual wall thickness meets design requirements:
- Processing Errors: Welding, cutting, and other processes may cause local thinning.
- Material Tolerance: Steel plates may have thickness tolerances (e.g., ±0.3–0.5 mm).
- Standard Requirements: Standards like GB/T 150 and ASME require a manufacturing deviation, typically set as Δ = 1–2 mm.
About Special Working Conditions
- How to Adjust Wall Thickness for High Temperatures?
High temperatures reduce material strength, so it is necessary to adjust the allowable stress ([σ]) based on temperature:
- Check the material’s high-temperature allowable stress at the design temperature and use it in the wall thickness formula.
- As temperature increases, allowable stress decreases, requiring thicker walls.
- For equipment running at high temperatures for long periods, consider creep effects. This may require increasing the wall thickness further or selecting high-temperature-resistant materials such as alloy steel or nickel-based alloys.
- How to Calculate Wall Thickness for Vessels Under External Pressure?
Vessels under external pressure must resist buckling (instability), and wall thickness calculations follow standard formulas:
- Use ASME BPVC or GB/T 150 external pressure methods to verify that the wall thickness meets stability requirements.
- Consider geometric parameters such as diameter and length, and use reinforcing structures like stiffening rings or ribs.
- External pressure vessels usually require thicker walls than internal pressure vessels to enhance buckling resistance.
- How to Ensure Uniform Wall Thickness in Large Pressure Vessels?
- Material Selection: Choose materials with high strength and good machinability to minimize overall thickness.
- Segmented Design: Use localized thickening or multi-layer designs for different stress zones.
- Welding Process Optimization: Ensure uniform welding joint strength and avoid stress concentrations that may lead to uneven thickness.
- Precision Equipment: Use automated cutting and heat treatment systems to reduce machining errors.
Conclusion
A well-designed wall thickness is crucial for ensuring the safety, durability, and cost-effectiveness of pressure vessels. Wall thickness depends on several factors, including design pressure, temperature, and material properties. It also requires careful consideration of corrosion allowance, manufacturing deviations, and welding quality under real working conditions. Whether you choose carbon steel, stainless steel, or high-performance nickel-based alloys, differences in allowable stress, temperature resistance, and corrosion resistance will directly affect the wall thickness design and the final performance of the equipment.
If you have any questions about wall thickness design, material selection, or other technical details of pressure vessels, feel free to contact us at any time. We offer professional technical guidance and can customize high-quality pressure vessels to meet your specific needs. Every product we deliver meets safety standards and process requirements. Choosing us means choosing superior quality and reliability. We look forward to working with you!