What factors are limiting the filling efficiency of CNG cylinders? Is it the bottleneck of equipment performance or the challenges of environmental conditions? Issues like overfilling, underfilling, or equipment failure quietly affect both the efficiency and safety of the filling process. Even worse, factors like aging equipment, unstable gas supply, and improper operations often combine to create inefficiencies. Many filling stations end up paying the price for slow filling, which impacts energy utilization and service quality.
During the CNG cylinders filling process, several factors can slow down the speed. Equipment limitations, changing environmental conditions, and complex workflows are common reasons for low efficiency. For example, outdated filling equipment may not support fast operations, while low ambient temperatures or poor gas quality can also disrupt the process. In addition, the experience of operators and the standardization of procedures directly affect how efficiently the filling is done.
This article will analyze the key factors that impact filling speed and offer practical solutions. These recommendations will help filling stations improve efficiency, solve common problems, and ensure smooth operations.
Why is the filling speed of CNG cylinders slow?
Equipment Issues
One major reason for the slow filling speed of CNG cylinders is equipment limitations. The CNG filling process requires high-pressure gas to move from the station’s storage system into the cylinder. During this process, the technology level, maintenance status, and performance of the equipment directly affect the filling speed.
Performance limits of the filling machine:
The pressurization capacity of the filling machine is a key factor for filling speed. If the compressor’s capacity is weak or the design has bottlenecks, gas cannot efficiently and quickly enter the cylinder. This is common in older filling equipment or when the configuration of the cylinder and filling machine does not match.
Equipment failures or wear and tear:
Any equipment failure can directly reduce filling efficiency. For example, leaking valves, inaccurate pressure sensors, or clogged pipelines can restrict gas flow during the process, slowing down the filling speed. Additionally, equipment that has been used for a long time may experience wear and tear, which reduces compression and storage efficiency during filling.
Cylinder compatibility issues:
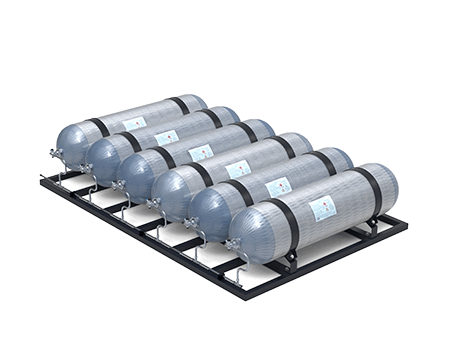
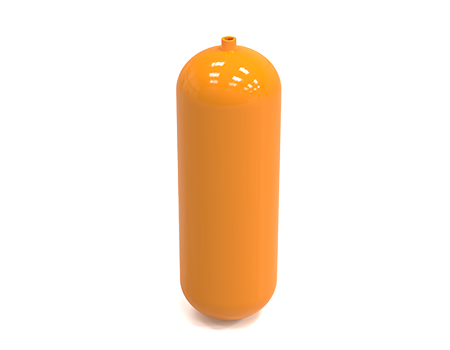
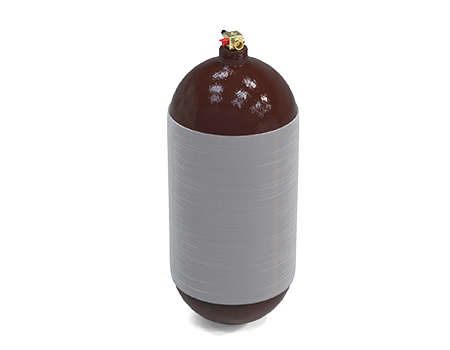
Different types and sizes of CNG cylinders require specific pressures and flow rates during filling. If the cylinders are not well-matched with the filling equipment, the filling speed may suffer. For instance, larger capacity cylinders require higher flow rates and pressure. If the equipment cannot provide enough compression power, the filling time will increase.
- Low-pressure cylinders: These generally operate at a working pressure of 200 bar (around 2900 psi). They are suitable for smaller cylinders (e.g., 10L, 15L) often used in small or light vehicles.
- High-pressure cylinders: Most commercial or heavy-duty vehicles use cylinders with a working pressure of 250 bar (around 3625 psi) or 300 bar (around 4350 psi). These are designed for larger cylinders (e.g., 40L, 50L, or more) that require higher filling pressure.
Environmental Factors
In addition to equipment issues, environmental factors can also affect the filling speed of CNG cylinders. These factors mainly include temperature, air pressure, and gas quality.
Ambient temperature:
CNG is stored as compressed gas, and the compression process is very sensitive to temperature. In low-temperature environments, gas compression efficiency drops significantly because the gas is more likely to condense, reducing its flow rate and slowing down the filling process. In high-temperature environments, although the gas flows better, the internal pressure in the cylinder can rise too quickly, which also slows down the filling process. Maintaining an optimal filling temperature is essential for improving filling speed.
External climate conditions:
If the gas source for the filling station comes from a distant storage tank or gas source station, the delivery process can be influenced by external conditions. For example, changes in weather can impact the pressure and flow rate of the gas supply. Cold weather, in particular, can reduce gas flow, leading to slower filling speeds.
Gas source quality:
The quality of the CNG source has a direct impact on the filling speed. If the gas contains a high percentage of impurities or moisture, it can clog filters or compressors in the filling system, reducing efficiency. Regular testing and treatment of the gas source are essential to ensure that the gas quality meets the required standards. This is a key measure to maintain consistent filling speeds.
Operational Process Issues
The operational processes and management methods of a filling station are also key factors that affect the filling speed. If the operations are not standardized or the management is disorganized, the filling process can become inefficient.
Improper operator handling:
The experience and skills of the filling station operators directly impact the filling speed. If operators are not familiar with standard procedures, they may make mistakes during the process. For example, setting the wrong filling pressure or inaccurate valve control can cause delays and extend the filling time.
Inadequate cylinder inspection and preparation:
Before filling, CNG cylinders must be inspected and prepared. If operators do not perform thorough checks, it can waste time and even compromise safety. For instance, inspecting residual gas levels, sealing conditions, and pressure status is crucial. Skipping or mishandling these steps can lead to unnecessary waiting time.
Complex processes:
Every step of the filling process can slow down the speed if it is not standardized or simplified. Tasks like loading and unloading cylinders, performing inspections, and managing labels can become bottlenecks if handled poorly. A well-designed process and clear operational guidelines can significantly improve the overall efficiency of the filling station.
Comprehensive Solutions to Improve Filling Efficiency and Prevent Common Issues
To improve the efficiency of CNG cylinder filling and avoid common problems, filling stations must make improvements in multiple areas, including equipment optimization, operational processes, and cylinder management. Below are comprehensive solutions designed to enhance filling efficiency and prevent issues. These solutions integrate Minno’s strengths in equipment optimization and technology applications, ensuring that the filling process is efficient, safe, and precise.
Equipment Optimization: Boosting Filling Efficiency
Filling equipment is the key to improving the efficiency of CNG cylinder filling. By optimizing equipment performance and ensuring long-term stable operation, filling speed can increase significantly, while energy consumption decreases. This also ensures the safety and precision of the filling process.
Enhancing the compression capacity of filling machines
The compression capacity of filling machines is crucial for increasing filling speed. This is especially important for large-capacity cylinders or high-pressure demands, where equipment capacity directly affects filling time. Minno’s filling equipment uses multi-stage compression technology, which effectively improves gas compression efficiency. It is particularly suitable for filling large-capacity, high-pressure cylinders, significantly reducing the filling time.
Regular maintenance and inspections
Over time, equipment can experience wear, dust accumulation, or loose components, which can impact normal operations and reduce filling efficiency. Minno’s equipment addresses these challenges with integrated filtration systems. Regular cleaning of gas filters prevents flow restrictions caused by dust buildup. In addition, pressure sensors and temperature sensors monitor abnormalities in real-time, issuing alerts to operators for timely maintenance. This prevents equipment failures from affecting the filling process.
Introducing intelligent equipment
Modern filling stations increasingly rely on smart equipment. Minno’s filling solutions integrate advanced sensors and data analysis systems to monitor key parameters in real-time, such as pressure, flow, and temperature. With automated control systems, the equipment adjusts filling speed and flow to meet the specific needs of different cylinders. The intelligent filling control system optimizes filling parameters automatically, reduces human error, and further enhances both efficiency and safety.
Preventing Common Issues: Ensuring Safe and Accurate Filling
During the filling process, common issues like overfilling, underfilling, interface leakage, and equipment failures can reduce efficiency and create safety risks. By implementing a series of effective measures, these problems can be prevented to ensure a smooth and secure filling process.
Preventing overfilling or underfilling
- Overfilling prevention: To avoid overfilling, Minno’s filling equipment features a high-precision pressure control system and an automatic stop function. When the internal pressure of the cylinder reaches the maximum set limit, the equipment stops filling automatically, preventing overpressure accidents. Regular calibration and inspection of the pressure control system also ensure its accuracy.
- Underfilling prevention: Minno’s filling systems come with an intelligent filling volume monitoring system, which tracks flow and cylinder capacity in real time. This ensures the required amount of gas is filled every time. The smart flow adjustment feature automatically regulates flow based on the cylinder’s remaining gas and filling requirements, avoiding underfilling caused by operator error.
Avoiding interface leakage
- Regular seal inspections: The seals and connections, such as valves and quick couplings, need regular checks to ensure proper sealing. Minno’s equipment uses high-performance sealing materials like fluororubber O-rings, which effectively prevent leaks and improve durability at connection points.
- Gas leakage detection system: Minnuo’s filling machines are equipped with an automatic leakage detection system that monitors changes in gas flow in real time. It can quickly identify interface leaks and send alarms, preventing safety hazards caused by leakage.
Preventing equipment failures
- Regular maintenance and intelligent self-checks: Minno’s systems include an intelligent self-diagnosis feature, which automatically checks the equipment’s operational status and provides early warnings for maintenance. Regular inspections of critical components such as compressors, valves, and sensors reduce the likelihood of failures, ensuring smooth and safe filling operations.
- High-quality components: To ensure long-term stable operation, Minno uses high-quality parts from internationally renowned brands. For example, Honeywell pressure sensors, Fuji high-efficiency compressors, and Heidenhain encoders from Germany. These premium components guarantee the equipment’s efficiency and reliability.
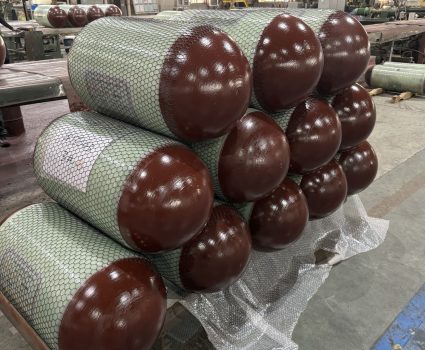
Conclusion
By analyzing the various factors affecting the CNG cylinder filling process, it is clear that improving filling efficiency is not simply about “speeding up” the operation. It requires optimization in multiple areas, including equipment performance, environmental conditions, and operational processes. To enhance filling efficiency, Minnuo has focused on optimizing equipment performance, integrating intelligent systems, and conducting regular maintenance. These efforts have significantly improved compressor efficiency, reduced filling times, and ensured stable equipment operation.
Our high-precision control systems effectively prevent overfilling, underfilling, and leakage, ensuring both safety and accuracy during the filling process.
If you have any questions or would like more information, feel free to visit our website. Our professional team is ready to provide customized solutions and support to help you improve filling efficiency and ensure smooth operations.