In the overall framework of industries such as chemicals, pharmaceuticals, and numerous other sectors, reactors play an indispensable and crucial role, serving as a fundamental support for the entire process. Among these, glass-lined reactors and stainless steel reactors, with their outstanding performance and excellent adaptability, have become core equipment widely used in the industry. They provide the essential environment for various chemical reactions, taking on the critical tasks of holding materials, creating suitable reaction conditions, and ensuring the orderly progression of the reaction. From the initial raw material input to the successful production of the final product, the entire process heavily relies on these two types of reactors, making them key elements in ensuring the smooth operation of industrial production.
Among the various types of reactors, glass-lined reactors and stainless steel reactors stand out with their distinct advantages and differences. Glass-lined reactors, made by applying a glass enamel coating to a metal substrate, exhibit exceptional corrosion resistance, protecting reactions involving highly corrosive media such as strong acids, alkalis, and organic solvents. However, they are brittle and prone to cracking or peeling under impact or rapid temperature changes, which can affect their stability. On the other hand, stainless steel reactors, made from iron-based alloys with added elements, offer high strength, resistance to high pressure, and ease of processing. However, they can be susceptible to corrosion in environments with high concentrations of chloride ions, requiring careful material selection.
This article aims to thoroughly analyze the differences between glass-lined and stainless steel reactors in terms of usage scenarios, performance characteristics, and other key factors. This article aims to thoroughly analyze the differences between glass-lined and stainless steel reactors. It will focus on usage scenarios, performance characteristics, and other key factors.
Core Differences Between Glass-Lined Reactors and Stainless Steel Reactors
The fundamental difference in materials leads to distinct performance characteristics:
- Glass-Lined Reactors: These are composite materials formed by fusing a layer of glass enamel onto a metal substrate. They exhibit excellent corrosion resistance, capable of withstanding the effects of most strong acids, alkalis, and organic solvents. However, they are brittle and can suffer from glass layer cracking or peeling under impact or sudden temperature changes, which can compromise their functionality.
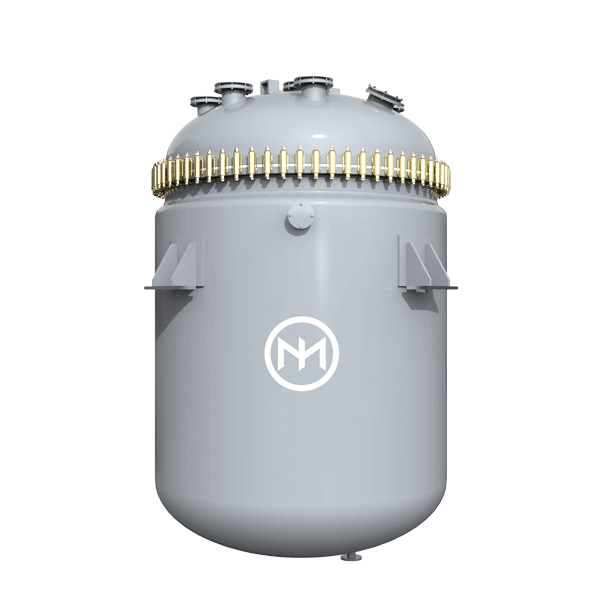
- Stainless Steel Reactors: Made from iron-based alloys combined with various other elements, stainless steel reactors offer high strength, resistance to high pressure, and ease of manufacturing. However, they are susceptible to corrosion in environments with high concentrations of chloride ions, requiring careful material selection to ensure their durability in specific chemical conditions.
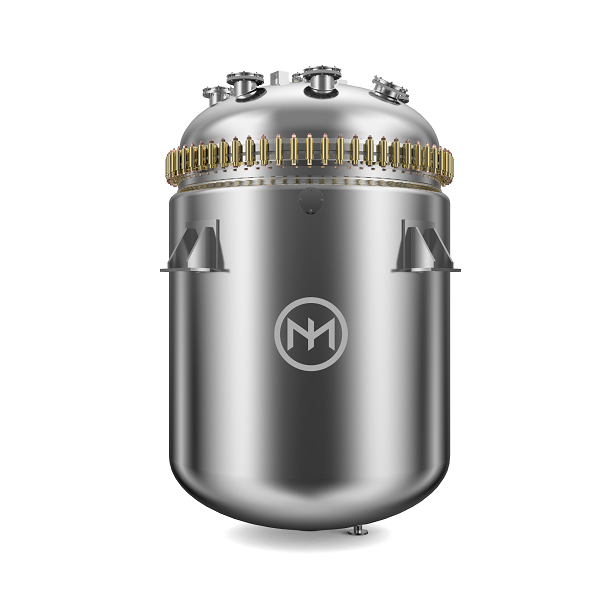
Differences in Process Requirements Between Glass-Lined and Stainless Steel Reactors
Impact of Strong Acids, Alkalis, and Solvents:
For chemical processes involving strong acids, alkalis, or solvents (e.g., production of inorganic acids or alkali-based chemicals), glass-lined reactors are often the preferred choice due to their excellent corrosion resistance. The glass lining can withstand strong acids and alkalis. This ensures safe and stable reactions, prolongs the reactor’s lifespan, and maintains product quality.
Tip: In acid environments with low concentrations (e.g., <5% hydrochloric acid, <10% sulfuric acid) and temperatures below 60°C, 316L stainless steel reactors, thanks to their passive oxide layer, can resist acid corrosion, e.g., in sulfuric acid sulfonation. In alkaline environments, 904L stainless steel, due to its high nickel content, can resist alkali corrosion in moderate concentrations and temperatures, suitable for organic alkali synthesis.
Choice for Organic Solvent Processes:
When using organic solvents that are highly permeable or corrosive to metals, glass-lined reactors are more suitable. This is due to their excellent barrier properties. However, in cases where organic solvents like fluorinated solvents can attack glass, specially treated stainless steel reactors or specific alloys can be used. The selection should depend on the chemical properties of the solvent.
Cross-Applicability of Both Reactors:
In neutral or weakly corrosive environments for organic synthesis (e.g., pH 6–8 without aggressive ions), both glass-lined and stainless steel reactors can be used. For example, 304 stainless steel is suitable for general organic syntheses like esterification (100–200°C, mild acidity), while 316 stainless steel performs well in mildly corrosive environments with low chloride ions (<1000ppm). Glass-lined reactors are ideal for reactions where the medium does not attack the glass lining, such as aromatic compound alkylation. In mild environments (pH 6.5–7.5, temperature 80–180°C), both reactors can be used in processes like simple carbonyl compound additions.
Temperature and Pressure as Key Decision Factors:
Under high-temperature and high-pressure conditions, stainless steel reactors have a clear advantage due to their high strength, thermal resistance, and ability to withstand mechanical stresses. They are crucial for processes like hydrogenation in the petrochemical industry. In these processes, temperatures can reach several hundred degrees, and high pressures are involved.
Glass-lined reactors, however, are prone to cracking at high temperatures due to the difference in thermal expansion between the glass and metal substrate. Their brittleness is also a limitation under high pressure, making them unsuitable for high-temperature and high-pressure processes. Yet, in moderate conditions, they excel in corrosion resistance and purity, suitable for fine chemical processes with less demanding temperature and pressure requirements.
Cleanliness and Safety Standards:
In industries like food and pharmaceuticals, where material cleanliness and safety are critical, glass-lined reactors are preferred due to their smooth interior surface, which resists material adsorption and is easy to clean and disinfect. Their chemical stability ensures no harmful substances are released, maintaining product quality.
Stainless steel reactors, especially those made from 316L food-grade or pharmaceutical-grade stainless steel, are also widely used. They offer good corrosion resistance and biocompatibility, meeting hygiene standards while supporting frequent cleaning and disinfecting. The choice of reactor material should consider both industry standards and the specific process requirements, such as temperature control precision and reaction pressure.
Comparison Dimension | Glass-Lined Reactor | Stainless Steel Reactor |
Initial Investment | Slightly lower price, suitable for small-scale applications with simple processes and mild corrosion, manufacturing costs are controllable. | Higher investment, can choose high-standard materials, suitable for complex processes. |
Long-Term Usage Cost | High brittleness, glass lining prone to damage, requiring frequent maintenance and repair, including re-lining, which impacts production schedule and increases costs. Overall cost is not advantageous. | Good durability, low maintenance, suitable for long-term production in large chemical enterprises, with lower repair and replacement costs and better economic benefits. |
Maintenance-Related Hidden Costs | Vulnerable to damage during transportation, installation, and usage due to external force or temperature/pressure changes. Maintenance is complex, requiring specialized personnel and specific conditions, with expensive re-lining; delays may also lead to penalty costs. | Strong durability, only requires routine inspection, cleaning, and maintenance, reducing downtime, improving production efficiency, and resulting in a low lifecycle cost. The initial investment is justified. |
Analysis from the Perspective of Operation and Maintenance
Is there a difference in the operational difficulty between glass-lined and stainless steel reactors?
Glass-lined reactors are more challenging to operate due to the fragile nature of the glass lining. Extra caution is required during loading and unloading. It is important to control material flow rates and directions to prevent impact on the reactor walls. Stirring must also be carefully monitored, with attention to the speed and position of the agitator to avoid collisions. This requires high standards of operation and attention to detail from the operators.
Stainless steel reactors are easier to operate, as the structure is stronger and can withstand certain external forces. However, for high-temperature, high-pressure processes, operators must strictly follow protocols to control parameters like temperature and pressure to ensure safe reactions.
Complexity of Daily Maintenance
How to prevent glass lining damage or peeling?
- Enhanced Regular Inspection: Develop a routine inspection plan. After each reaction, promptly check for signs of cracks or peeling using a flashlight or borescope.
- Standardized Cleaning Procedures: Use soft tools like soft brushes or sponges, avoid sharp objects. Clean from top to bottom and rinse thoroughly with clean water to remove any cleaning agent residue.
- Controlled Installation and Disassembly: When installing or removing agitators, thermometers, etc., position them accurately and install/disassemble slowly. Use a torque wrench to control tightening force and avoid excessive pressure.
- Optimized Transport and Storage: Use shock-absorbing tools during transport, secure the reactor properly, and use soft materials for cushioning. Store in a dry, ventilated area, and if stored for a long time, use nitrogen gas to maintain stability.
How to address corrosion and cleaning issues in stainless steel reactors?
Corrosion Protection:
- Material Selection: Choose appropriate stainless steel grades based on the chemical environment.
- Regular Inspection: Periodically check the reactor surface for corrosion, particularly at welds and seals.
- Protective Measures: Apply protective coatings or electrochemical protection to vulnerable areas.
Cleaning and Maintenance:
- Cleaner Selection: Use suitable cleaning agents and avoid cleaners containing corrosive substances like chloride ions.
- Cleaning Process: Follow proper cleaning procedures to ensure thorough cleaning. When switching between different products, ensure no residue is left to avoid cross-contamination.
What to Do When the Chemical Properties of the Medium Are Uncertain?
When the chemical properties of the medium are uncertain, the following steps can be taken:
- Conduct a simple preliminary experiment by exposing a small sample of the medium to the reactor material. Observe for any corrosion or discoloration to make a preliminary compatibility judgment.
- Refer to chemical handbooks, industry resources, or consult professional chemical engineers to understand how similar media have interacted with reactors in past applications.
- During trial production or small-scale R&D experiments, prioritize using a versatile glass-lined reactor. Its excellent corrosion resistance will help in determining the medium’s properties and making precise material selection.
Conclusion: How to Choose the Right Reactor
When selecting a reactor, it is crucial to balance your requirements and budget. A comprehensive evaluation of process conditions, economic costs, and maintenance needs is necessary. Don’t worry—Minnuo is here to help! With a wide range of selection options and expert consultation services, Minno will guide you in pinpointing the most suitable equipment, ensuring smooth and worry-free production.