In today’s industrial landscape, innovation drives progress across sectors like energy, pharmaceuticals, and food production. Among the critical equipment used in these industries is the stainless steel reactor, known for its strength and reliability. Whether for chemical processing or energy production, this reactor type is a key player in ensuring safety, efficiency, and durability in challenging environments.
A stainless steel reactor is a robust vessel used for conducting chemical reactions under controlled conditions. Made from corrosion-resistant stainless steel, it is ideal for handling reactive substances at high temperatures and pressures, making it essential for industries like pharmaceuticals, petrochemicals, and food processing.
In this article, we will explore the different types of stainless steel reactors, the different materials used, and the many applications they offer. By reading this article, you will have a clear understanding of how to choose the right reactor for your needs and how this type of equipment can help you achieve the best production results.
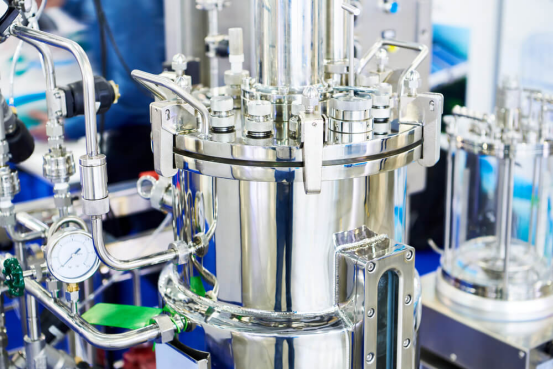
What is a Stainless Steel Reactor?
Definition and Purpose
A stainless steel reactor is a specialized vessel designed to carry out chemical reactions in a controlled environment. These reactors are made of stainless steel, which provides the necessary durability, corrosion resistance, and strength to handle a wide range of chemical processes. They are used in various industries, from pharmaceuticals to chemical manufacturing, to create products through controlled reactions involving different materials.
The primary functions of a stainless steel reactor include:
- Mixing: Ensuring that the reactants are thoroughly combined to allow for a uniform chemical reaction. Agitators or mixers are often employed to achieve optimal mixing conditions.
- Heating: Many chemical reactions require precise temperature control to ensure they proceed at the correct rate. A stainless steel reactor typically includes heating jackets or internal heating coils to regulate temperature.
- Cooling: Some reactions release heat or occur exothermically, and to prevent overheating or to maintain an ideal temperature range, cooling systems are incorporated to remove excess heat.
- Pressure Control: Reactions may need to occur under specific pressure conditions, particularly in reactions that produce gases or involve volatile substances. Pressure monitoring and regulation equipment ensure that the reactor stays within safe and optimal pressure limits.
- Reaction Monitoring: Reactors are equipped with various sensors and instrumentation to monitor important parameters such as pressure, temperature, pH, and reaction time, ensuring the reaction proceeds as planned and any deviations can be corrected in real time.
Applications of Stainless Steel Reactors
Stainless steel reactors are used in a wide range of industries, owing to their versatility and ability to operate under challenging conditions. Some of the most common applications include:
Pharmaceutical Industry:
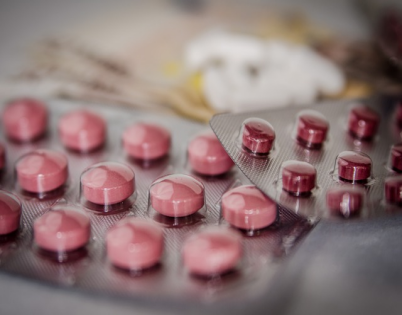
Stainless steel reactors play a crucial role in drug synthesis, fermentation, and other pharmaceutical processes. For example, they are used to produce Active Pharmaceutical Ingredients (APIs) in controlled environments, ensuring high-quality products that meet strict regulatory standards. Stainless steel’s ability to resist contamination and corrosion makes it ideal for maintaining the purity of pharmaceutical products. Common processes include:
- Drug Synthesis: Combining raw materials to create compounds used in medications.
- Fermentation: Producing biologically active compounds or pharmaceuticals through the fermentation of microorganisms.
Chemical Processing:
In chemical processing, stainless steel reactors are essential for complex reactions such as polymerization, oxidation, reduction, and hydrogenation. These reactions often require the reactor to handle extreme temperatures, pressures, and corrosive chemicals. Some specific applications in this field include:
- Polymerization: The formation of polymers from monomers, which is critical in manufacturing plastics and other materials.
- Oxidation Reactions: Used in producing chemicals like acetic acid, alcohols, and other oxidized compounds.
Food and Beverage Production:
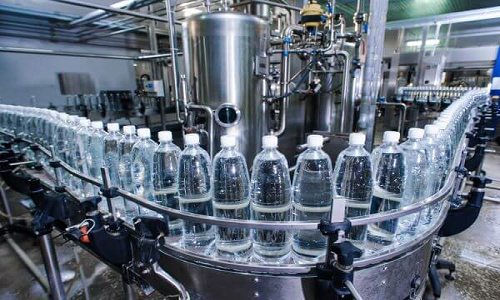
Stainless steel reactors are extensively used in the food and beverage industry for processes such as fermentation and pasteurization. Fermentation, a process by which microorganisms convert sugars into alcohol or acids, is crucial in the production of products like beer, wine, and yogurt. Similarly, pasteurization, the process of heating food to kill harmful bacteria while preserving its nutritional value, is often carried out in stainless steel reactors. Key applications include:
- Fermentation: Creating products like alcohol, dairy, and probiotics.
- Pasteurization: Ensuring food safety while maintaining product quality.
Energy and Environmental Sectors:
Stainless steel reactors also play a significant role in the energy and environmental sectors. In biodiesel production, for instance, stainless steel reactors are used to catalyze the conversion of vegetable oils or animal fats into biodiesel. Similarly, in waste-to-energy processes, these reactors help in converting organic waste into usable energy through processes like anaerobic digestion. Other applications in this sector include:
- Biodiesel Production: Converting renewable oils into biodiesel for use as an alternative fuel.
- Waste-to-Energy: Converting municipal or industrial waste into energy, often through biological or chemical processes.
Types of Stainless Steel Reactors
Understanding the different types of stainless steel reactors is essential for determining which one best suits your production needs. Reactors can generally be classified based on their operational method, which includes batch, continuous, semi-batch, and pilot reactors. Each of these types is designed for specific processes, offering various benefits depending on the scale of production, the complexity of the reaction, and the nature of the product. Below, we explore these four main types in more detail.
Batch Reactors
Batch reactors are designed to process a specific quantity of reactants at a time, where the reaction is carried out in a closed environment for a set duration. The process involves loading the reactor with raw materials, allowing the reaction to occur for a predetermined amount of time, and then unloading the final product. After completing one batch, the reactor is emptied, cleaned, and refilled for the next cycle. This process is not continuous but occurs in discrete steps.
Advantages:
- Flexibility: Batch reactors offer significant flexibility in terms of the types of reactions that can be processed and the scale of production. They are ideal for small-to-medium quantities and various batch sizes.
- Control: Operators have greater control over reaction time, temperature, and other parameters, allowing for fine-tuning during the process.
- Cleaning: It’s easier to clean and sanitize between batches, which is particularly important in industries like pharmaceuticals or food production, where contamination control is critical.
- Cost-Effective for Smaller Quantities: For small or medium-scale production, batch reactors generally have lower operational costs compared to continuous reactors.
Continuous Reactors
Continuous reactors are designed for large-scale operations where reactants are continuously fed into the reactor and products are continuously removed. Unlike batch reactors, the reaction in a continuous reactor never stops, enabling an uninterrupted production process. This setup is ideal for high-volume manufacturing and processes where the reaction time is predictable and consistent.
Advantages:
- Efficiency: Continuous reactors are highly efficient for large-volume production, as they can operate continuously without the need to stop for cleaning or reloading.
- Consistent Quality: The constant flow of reactants and products allows for uniform reaction conditions, which helps maintain consistent product quality.
- High Throughput: With the ability to process large volumes over extended periods, continuous reactors offer higher throughput and productivity.
- Lower Labor Costs: Due to automation and continuous operation, continuous reactors reduce the need for labor-intensive monitoring and intervention.
Pilot Reactors
Pilot reactors are smaller-scale versions of industrial reactors used primarily in research and development or for process optimization. They are typically employed to simulate industrial-scale reactions before scaling up to full production. Pilot reactors allow manufacturers to test reaction parameters, observe results under controlled conditions, and refine the process before committing to large-scale production.
Advantages:
- Lower Investment: Pilot reactors are less expensive to install and operate compared to full-scale industrial reactors, making them ideal for testing new processes or formulations.
- Experimental Flexibility: These reactors allow for experimentation with different operating conditions, such as temperature, pressure, and feed rates, without the risk and cost of industrial-scale production.
- Scalability: Successful results from pilot-scale reactors can be used to design and scale up to full production, reducing risk during the transition to industrial-scale operations.
Semi-Batch Reactors
Semi-batch reactors combine elements from both batch and continuous reactors. Reactants are added either continuously or in stages during the reaction, but the reaction itself takes place in a batch-wise manner. This hybrid setup provides the benefits of continuous input while maintaining the flexibility and control typical of batch processes. Semi-batch reactors are often used when the reaction is sensitive to the concentration of reactants or requires more precise control over the reaction rate.
Advantages:
- Increased Control: Operators can precisely control the rate at which reactants are added, improving the overall control over the reaction process.
- Adaptability: These reactors are adaptable to varying feed rates, making them suitable for processes that require a fluctuating supply of materials.
- Reduced Reaction Time: Compared to traditional batch processes, semi-batch reactors often allow for shorter reaction times, improving overall production efficiency.
Materials of Stainless Steel Reactors
The material chosen for a stainless steel reactor plays a crucial role in determining its longevity, performance, and overall efficiency. When selecting a reactor material, several factors must be considered, including chemical exposure, operating temperatures, mechanical properties, and environmental conditions. Stainless steel, known for its excellent corrosion resistance, strength, and versatility, is the most common material used in reactor construction. However, within the category of stainless steel, different grades offer varying levels of performance depending on the specific needs of the process.
Grades of Stainless Steel for Reactors
Different grades of stainless steel offer unique advantages depending on the type of process and the chemicals involved. The three most commonly used grades for stainless steel reactors are 304, 316, and 2205 Duplex.
304 Stainless Steel
304 stainless steel is the most commonly used grade in various industries, including food, pharmaceuticals, and chemical processing. It is a general-purpose alloy that offers a good balance of corrosion resistance, strength, and formability.
Pros:
- Corrosion Resistance: 304 stainless steel provides excellent resistance to a wide range of chemicals and atmospheric conditions, making it suitable for general-purpose applications.
- Weldability: It is easy to weld, making it ideal for reactors that need to be assembled or modified.
- Cost-Effective: One of the more affordable stainless steel grades, 304 stainless steel is a budget-friendly option for many standard applications.
Cons:
- Limited Resistance to Extreme Conditions: While 304 stainless steel offers good general corrosion resistance, it does not perform well in highly aggressive environments, such as exposure to concentrated acids, chlorides, or elevated temperatures.
- Less Suitable for Harsh Chemicals: Reactors exposed to high levels of aggressive chemicals, like hydrochloric acid or sulfuric acid, may require a more resistant material.
Applications:
- General-purpose reactors where exposure to mild chemicals is expected.
- Food and beverage production.
- Pharmaceutical manufacturing (where less aggressive chemicals are used).
316 Stainless Steel
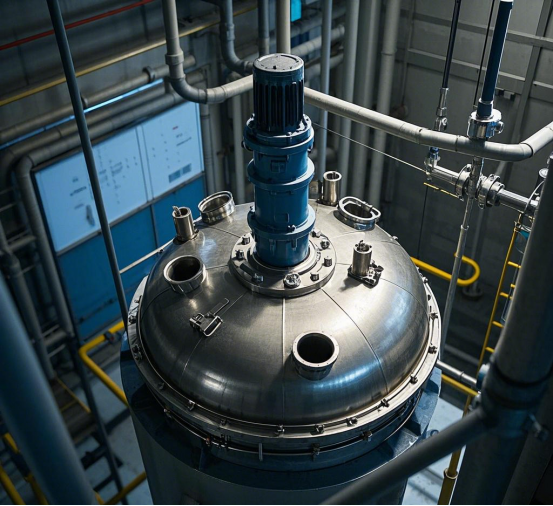
316 stainless steel is a highly corrosion-resistant alloy, often considered the best choice for reactors operating in harsh environments. It is particularly useful when reactors are exposed to chlorides, acids, or other corrosive agents.
Pros:
- Superior Corrosion Resistance: 316 stainless steel is particularly resistant to chloride-induced corrosion, making it ideal for use in marine environments and highly corrosive chemical processes.
- Better Performance Under High Temperatures: This grade performs better than 304 in high-temperature environments and in contact with aggressive chemicals.
- Weldability: Like 304, 316 stainless steel is highly weldable, allowing for efficient reactor assembly and repair.
Cons:
- Higher Cost: 316 stainless steel is more expensive than 304 due to its higher molybdenum content, which provides superior corrosion resistance.
- Cost Considerations for Less Demanding Applications: If the reactor will not be exposed to aggressive chemicals or extreme temperatures, the additional cost of 316 stainless steel may not be justified.
Applications:
- Pharmaceutical reactors (where precise and safe chemical reactions are critical).
- Food and beverage reactors (particularly in environments exposed to chlorides or acids).
- Chemical reactors that deal with harsh or corrosive chemicals, such as sulfuric acid, chlorides, or seawater.
2205 Duplex Stainless Steel
2205 duplex stainless steel is a high-performance alloy that combines the advantages of both austenitic and ferritic stainless steels. It is especially suitable for reactors used in highly demanding environments where both strength and resistance to corrosion are critical.
Pros:
- Superior Strength: Duplex stainless steel offers a higher strength-to-weight ratio than both 304 and 316, making it an excellent choice for pressure vessels and reactors requiring high strength.
- Excellent Resistance to Stress Corrosion Cracking: 2205 is highly resistant to stress corrosion cracking, pitting, and crevice corrosion, making it ideal for harsh chemical processes.
- Good Performance in Extreme Conditions: This alloy performs well under high pressures and temperatures, offering superior durability in tough industrial environments.
Cons:
- Higher Cost: Duplex stainless steel is more expensive than both 304 and 316 stainless steel, which may make it less suitable for applications where cost is a primary concern.
- Difficult to Weld: While 2205 is highly resistant to corrosion, it is more challenging to weld than other stainless steel grades, requiring special procedures and skilled technicians.
Applications:
- Reactors in high-stress, high-temperature environments, such as chemical plants and offshore oil rigs.
- Pressure vessels and reactors dealing with aggressive chemicals like sulfuric acid, chlorides, and other corrosive substances.
- Applications requiring both high strength and exceptional resistance to corrosion.
Choosing the Right Stainless Steel for Your Reactor
When choosing the right grade of stainless steel for your reactor, several factors must be considered to ensure optimal performance and longevity:
- Chemical Exposure: Consider the types of chemicals the reactor will be exposed to. If you are dealing with highly corrosive substances, a more corrosion-resistant alloy like 316 or 2205 duplex may be necessary. For less demanding applications, 304 may suffice.
- Operating Temperature: Higher temperatures can accelerate corrosion and decrease the material’s strength. For reactors operating in elevated temperature environments, 316 or 2205 duplex stainless steel may provide better long-term performance.
- Mechanical Properties: The reactor’s design and pressure requirements will influence the selection of stainless steel. If strength and durability are critical, consider using duplex stainless steel (2205), as it has a higher strength-to-weight ratio compared to 304 and 316.
- Environmental Conditions: Humidity, moisture, and pH levels can significantly affect material selection. For example, reactors exposed to harsh marine environments or chemical plants with fluctuating pH levels may require more resistant materials like 316 or 2205 duplex stainless steel.
Other Materials for Reactor Linings or Coatings
In some specialized applications, additional linings or coatings may be used to further protect the reactor from corrosion or chemical attack. Common materials for reactor linings include:
- Glass-Lined Reactors: These reactors have an inner lining of glass, offering excellent resistance to corrosive chemicals, particularly in industries like pharmaceuticals and food processing. The glass lining helps protect the stainless steel from harsh acids and alkalis.
- Titanium Coatings: Titanium is highly resistant to corrosion, especially in environments with strong acids and chlorides. It is often used in reactors where stainless steel may not offer adequate protection.
- Ceramic Coatings: Ceramic coatings can be applied to reactors to provide a hard, chemically inert surface. This can enhance the resistance to abrasive or highly reactive chemicals, making it a good option for some chemical processing applications.
These additional linings or coatings provide an extra layer of protection, improving the durability and life cycle of reactors exposed to extreme conditions. Industries that deal with particularly aggressive chemicals, such as pharmaceuticals or specialized chemical processes, may opt for such coatings to ensure both safety and operational efficiency.
Key Features to Look for in Stainless Steel Reactors
Pressure and Temperature Control
Accurate Pressure and Temperature Regulation
Pressure and temperature are two of the most critical variables that determine the success of any chemical reaction. For a stainless steel reactor to function efficiently, it must be equipped with precise pressure and temperature control mechanisms. These controls ensure that the reactor operates under optimal conditions, which can significantly affect reaction rates, product quality, and safety.
Why It Matters:
- Safety: Without proper control, excessive pressure or temperature could lead to unsafe situations such as explosions, overheating, or equipment failure. Reactors must be able to maintain pressure and temperature within safe limits.
- Consistency: Consistent reaction conditions help ensure repeatability and consistency in the production process. Inconsistent temperature or pressure can lead to unwanted by-products, poor yields, or batch variability.
- Performance: Precise regulation leads to better reaction efficiency, faster processing times, and better control over end product quality.
What to Look for:
- Pressure Sensors and Gauges: Ensure that the reactor is equipped with reliable sensors that monitor internal pressure and provide real-time data.
- Temperature Sensors: Look for reactors with accurate temperature sensors to maintain the desired operating range.
- Automated Control Systems: Automated control systems, such as PID (Proportional-Integral-Derivative) controllers, allow for precise adjustments to pressure and temperature, ensuring that the reaction environment remains stable and within safe limits.
Mixing and Agitation Systems
Uniform Mixing for Optimal Reactions
The success of many chemical reactions depends on the thorough mixing of reactants. Incomplete or inefficient mixing can lead to incomplete reactions, uneven product quality, and lower yields. An efficient mixing system is crucial for achieving uniform temperature and concentration throughout the reactor, thus ensuring consistent and high-quality outcomes.
Why It Matters:
- Reaction Efficiency: Effective mixing helps ensure that all reactants come into contact with each other, enabling complete reactions and reducing the risk of side reactions.
- Heat Distribution: A well-designed agitation system ensures uniform temperature distribution, preventing hot spots that could lead to degradation of sensitive materials or inefficient reaction kinetics.
- Viscosity Considerations: For reactors dealing with highly viscous materials, the agitation system must be robust enough to handle the increased resistance to flow and ensure effective mixing.
What to Look for:
- Mechanical Stirrer or Impeller Systems: For most general-purpose reactions, a mechanical stirrer (e.g., an anchor or turbine impeller) will suffice. The choice of impeller design and speed should be based on the process requirements.
- Magnetic Stirrer Systems: In smaller reactors or when contamination needs to be avoided, magnetic stirrers are a viable option. These systems use magnets to drive stirrers without physical contact.
- Pneumatic Agitation: For certain types of reactors, especially in high-viscosity applications, pneumatic agitation can offer effective mixing by using compressed air to move stirrers.
Sealing and Safety Features
Preventing Leaks and Ensuring Safe Operations
The integrity of the reactor seals is crucial in preventing leakage of volatile or hazardous chemicals. Reactors should have high-quality gaskets and seals to prevent contamination or the escape of gases and liquids under pressure. Additionally, safety features that protect against pressure surges, over-heating, and explosive reactions are essential for ensuring worker safety and preventing damage to the equipment.
Why It Matters:
- Chemical Safety: Leaks can lead to contamination of the product, the environment, and even pose health risks to workers. Proper seals prevent such issues by keeping volatile chemicals contained.
- Explosion Protection: Reactors handling hazardous chemicals under high pressure and temperature need to be equipped with safety features to prevent catastrophic failure. This includes pressure relief valves, explosion-proof designs, and emergency venting systems.
- System Integrity: High-quality seals and gaskets ensure the reactor remains leak-free and maintains its structural integrity during operation, contributing to better overall performance and longevity.
What to Look for:
- Pressure Relief Valves: These valves are essential for venting excess pressure and preventing dangerous over-pressurization that could lead to catastrophic failure.
- Explosion-Proof Designs: Ensure that the reactor is designed to withstand unexpected pressure surges or thermal events.
- High-Quality Gaskets and Seals: Check that seals are made from durable, high-quality materials like PTFE, Viton, or other chemically resistant polymers, which are designed to withstand high pressures and temperatures.
Customization
Tailored Features for Specific Process Needs
Not all chemical processes are the same, and sometimes a standard reactor might not meet the specific requirements of a given application. Customizable reactors allow industries to modify certain features based on their process needs, such as reactor size, material construction, heating/cooling options, and agitation systems.
Why It Matters:
- Process Optimization: Tailored reactors ensure that each aspect of the reactor is designed specifically for the chemical process in question, resulting in greater efficiency, safety, and product quality.
- Flexibility: Customization allows industries to adapt to changing production requirements or upgrades without needing a completely new system.
- Efficiency Gains: By selecting specific reactor sizes, materials, and configurations, manufacturers can improve reaction kinetics, energy consumption, and process throughput.
What to Look for:
- Reactor Size: Choose a reactor that can handle the required volume of materials while maintaining efficiency and safety.
- Jacketed Heating or Cooling Systems: Custom reactors can include jacketed systems for controlled heating or cooling, which is critical for reactions that require precise temperature control.
- Material of Construction: Beyond stainless steel, reactors can be customized with materials such as Hastelloy, titanium, or glass linings depending on the chemical compatibility needed.
- Agitation System Type: The design and type of agitation system should be tailored to the viscosity and mixing requirements of the materials being processed.
Conclusion :
Stainless steel reactors are essential for efficient, safe, and durable chemical reactions in industries like pharmaceuticals and food processing. Their corrosion resistance and reliability make them a top choice for handling demanding processes.
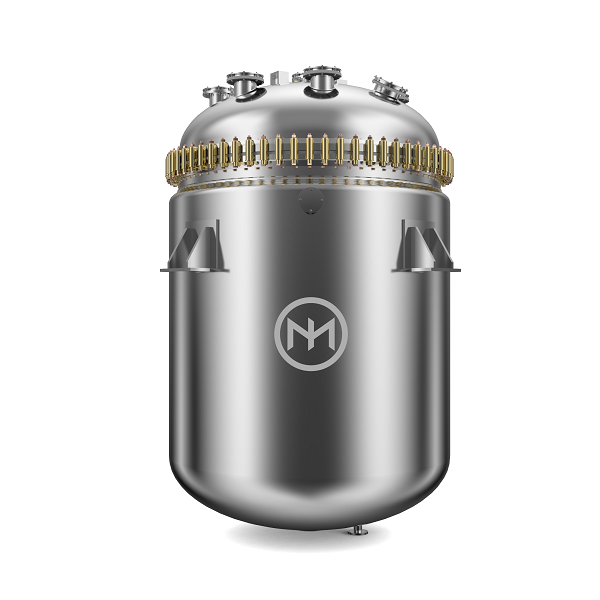
If you’re looking for the best stainless steel reactors to elevate your operations, don’t wait—contact us now! Our expert team is eager to help you find the perfect solution and drive your success forward.