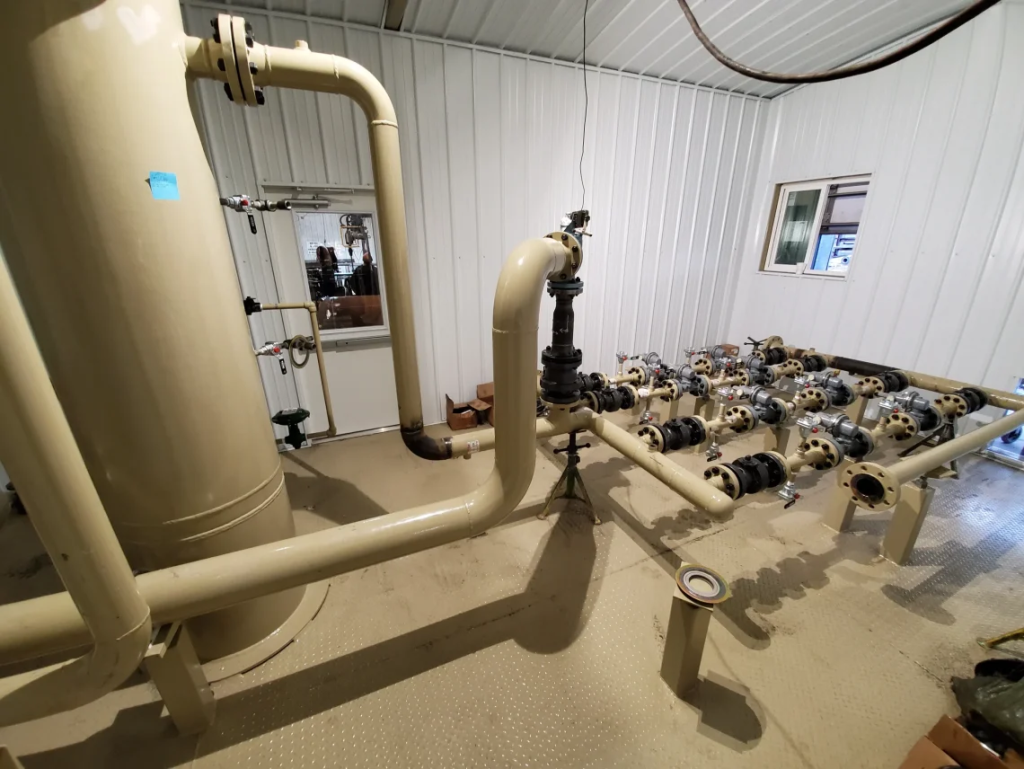
Recently, with the acceleration of global energy transition, especially the rise of renewable energy and low-carbon technologies, traditional energy industries are facing significant challenges. In high-risk sectors such as oil, gas, and chemicals, ensuring the safety and reliability of equipment has become a key concern. Pressure vessels and pipes play a crucial role in these industries, but many still have doubts about the differences between them. Especially when it comes to handling and transporting pressurized fluids, while pipes and pressure vessels have similar functions, they differ significantly in design and application. Today, we will explore the question: Are pipes considered pressure vessels?
The answer is: No, pipes are not pressure vessels. Although both involve carrying pressurized fluids, pipes are primarily designed for transporting fluids, whereas pressure vessels are designed for storing or processing high-pressure fluids. Pressure vessels are specifically engineered to withstand very high internal pressures, while pipes are not built to handle such extreme pressure conditions.
In the following sections, we will delve into the technical differences between pipes and pressure vessels, their respective roles in various industries, and why accurate classification is so important.
Understanding Pressure Vessels
1.Definition of a Pressure Vessel
A pressure vessel is a container designed to hold gases or liquids at a pressure significantly different from the ambient pressure. These vessels are typically used in a variety of industrial applications, such as chemical processing, power generation, oil and gas, and manufacturing, to store or transport fluids under pressure. According to regulatory standards such as the ASME (American Society of Mechanical Engineers) Boiler and Pressure Vessel Code, a pressure vessel is defined as a closed container designed to withstand high-pressure conditions, typically above 15 psi (pounds per square inch), although this threshold can vary by industry and jurisdiction.
Pressure vessels can be cylindrical, spherical, or conical in shape, with the exact design dependent on the application and the pressures involved. The most common types include storage tanks, boilers, reactors, and heat exchangers.
2.Characteristics of Pressure Vessels
Pressure vessels possess several defining characteristics:
High Pressure: Pressure vessels are designed to withstand internal or external pressures that are significantly different from atmospheric pressure. The internal pressure may be generated due to a gas or liquid stored inside, and it can vary widely depending on the purpose of the vessel.
Thickness of Material: The walls of pressure vessels are typically thicker than those of regular containers in order to withstand the stresses generated by high pressure. The thickness is determined based on factors like the pressure inside, the material’s strength, and the vessel’s size.
Rigidity: Pressure vessels are generally designed to maintain structural integrity under various operating conditions, including temperature fluctuations, seismic activity, and mechanical stresses. This ensures that the vessel does not deform, rupture, or collapse under pressure.
Safety Systems: Pressure vessels often include built-in safety systems such as relief valves, pressure gauges, and rupture discs to prevent accidents or failures in case of overpressure. These systems are critical in ensuring the safe operation of the vessel.
Testing and Inspection: Pressure vessels are subjected to rigorous testing and regular inspections to verify their integrity. These include non-destructive testing methods such as ultrasonic testing, radiographic testing, and visual inspections to detect any flaws, cracks, or weaknesses.
3. Importance of Pressure Vessels in Industry
Pressure vessels are crucial in a wide range of industries because they enable the safe and efficient containment of high-pressure fluids, whether for storage, transportation, or processing. Their role is indispensable, especially in sectors where safety, efficiency, and operational continuity are paramount. Here are several reasons why pressure vessels are so important in industrial applications:
Chemical Processing:
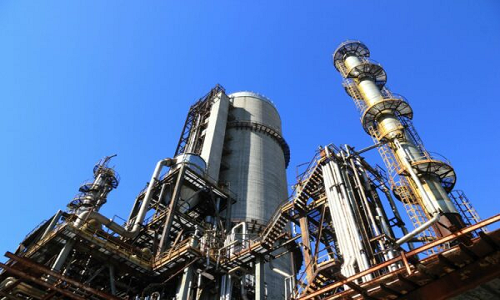
In industries like petrochemicals, pharmaceuticals, and food processing, pressure vessels are used for a variety of purposes such as reactors, distillation columns, and pressure tanks. They enable chemical reactions to occur under controlled high-pressure conditions, allowing for more efficient processing.
Power Generation:
Pressure vessels are used in steam boilers, heat exchangers, and other energy systems where high-pressure steam or fluids are necessary to generate power. In power plants, these vessels help optimize energy efficiency by controlling the pressure and temperature of steam, which is critical for generating electricity.
Oil and Gas:
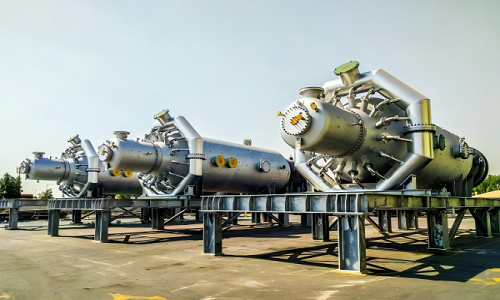
Pressure vessels play a central role in the extraction, transportation, and refining of oil and gas. These vessels store or transport gases under high pressure and maintain the integrity of crude oil and natural gas during extraction and processing.
Storage and Transportation:
Pressure vessels are widely used for the storage and transportation of liquefied gases, such as propane, oxygen, and ammonia. These vessels ensure that gases are stored safely at a controlled pressure, reducing the risk of leaks or explosions during transportation.
Safety and Regulation Compliance:
Given their critical function, pressure vessels must comply with rigorous industry regulations and safety standards. This ensures that they are built to withstand extreme conditions and that they are regularly inspected for signs of wear, corrosion, or damage. By adhering to these standards, industries can minimize the risks of catastrophic accidents and ensure that operations continue smoothly.
4. Safety Features in Pressure Vessel Design
The safety of pressure vessels is of paramount importance, given the potentially catastrophic consequences of a failure. For this reason, pressure vessel design incorporates several safety features that are designed to minimize the risk of accidents, protect workers, and maintain the integrity of the surrounding infrastructure. Below are the key safety features commonly included in pressure vessel design:
Relief Valves and Safety Valves:
One of the primary safety features in pressure vessels is the inclusion of pressure relief valves (PRVs) and safety valves. These valves are designed to release excess pressure in the vessel if it exceeds a predetermined limit, thereby preventing rupture or explosion. These safety devices are critical for maintaining the integrity of the vessel and preventing overpressure-related incidents.
Rupture Discs:
A rupture disc is a safety device that is installed in parallel with a pressure relief valve. It acts as a backup system to prevent dangerous overpressure situations. If the pressure in the vessel exceeds a certain level, the rupture disc bursts, allowing the pressure to be safely relieved. Rupture discs are often used in conjunction with other safety devices for additional protection.
Pressure Gauges:
Pressure gauges are essential for monitoring the pressure inside a vessel in real-time. These gauges help operators maintain the pressure within safe operating limits. In many cases, pressure gauges are equipped with alarms to alert personnel if the pressure deviates from the desired range.
Vessel Materials:
The choice of material is critical to the safety of the pressure vessel. The material must be capable of withstanding the internal pressures without becoming brittle or cracking. Common materials used in pressure vessel construction include carbon steel, stainless steel, and specialized alloys. These materials are selected based on the type of fluid, temperature, and pressure involved in the application.
Corrosion and Fatigue Resistance:
Pressure vessels often operate under extreme conditions, which can lead to corrosion or material fatigue over time. Special coatings, corrosion-resistant alloys, and design modifications are used to prevent these issues and ensure the long-term integrity of the vessel.
Inspection and Testing:
Regular inspection and testing are essential to ensure the continued safety of pressure vessels. Non-destructive testing (NDT) methods such as ultrasonic, radiographic, and magnetic particle testing are commonly used to detect hidden defects or weaknesses. Routine pressure testing is also carried out to verify the vessel’s performance under expected operating conditions.
Redundant Systems:
In high-risk applications, pressure vessels may be equipped with redundant safety systems. For example, multiple pressure relief valves may be used in tandem to ensure that even if one system fails, the vessel remains protected.
Design Codes and Standards:
Pressure vessel designs follow strict codes and standards, such as the ASME Boiler and Pressure Vessel Code (BPVC). This code outlines the minimum design, construction, and testing requirements to ensure safety. These standards provide a blueprint for manufacturers and operators to follow, reducing the risk of accidents and ensuring that pressure vessels are built to withstand the rigors of operation.
Is a Pipe a Pressure Vessel?
No, a pipe is not considered a pressure vessel.
While both pipes and pressure vessels may handle pressurized fluids, they are fundamentally different in terms of design, function, and the pressures they are intended to withstand.
Elaboration:
Design and Function:
- Pipes are designed primarily to transport fluids from one location to another. Their function is to serve as conduits for the flow of liquids or gases, often under moderate pressure.
- Pressure vessels, on the other hand, are designed to contain and store fluids at high pressure within a confined space. Their role is not just to transport, but to safely hold fluids under significant pressure, often for storage or processing.
Pressure Levels:
- Pressure vessels are designed to withstand high internal pressures, often exceeding atmospheric pressure. Some operate in the range of hundreds or even thousands of psi (pounds per square inch).
- Pipes, although they may carry pressurized fluids, are generally not designed to withstand the extreme internal pressures that pressure vessels are built to endure.
Shape and Structure:
- Pressure vessels are typically cylindrical, spherical, or conical in shape. They are designed to handle stress and pressure from all directions within a confined space.
- Pipes are tubular and designed mainly for fluid flow. Their structural requirements are different, as they focus on being conduits for transport rather than containers for pressurized fluids.
Safety Features:
- Pressure vessels are equipped with extensive safety features, such as pressure relief valves, rupture discs, and reinforced materials to handle high internal pressures and ensure safe operation.
- While pipes may have some safety devices like valves and pressure monitoring, they are not subject to the same rigorous safety standards as pressure vessels, which are specifically designed to contain and control high-pressure conditions.
Regulatory Standards:
- Pressure vessels are regulated under specific codes such as the ASME Boiler and Pressure Vessel Code (BPVC), which ensures they are designed, tested, and maintained to safely handle high-pressure scenarios.
- Pipes, while also regulated (e.g., ASME B31.3 for pressure piping), do not face the same level of scrutiny in terms of pressure containment and structural integrity under extreme conditions.
Key Differences Between Pipes and Pressure Vessels
Pressure Levels:
Pressure vessels are designed to handle higher internal pressures than pipes. A pressure vessel typically operates with pressures exceeding atmospheric levels (above 15 psi). Depending on the application, pressures can range from hundreds to thousands of psi. Pipes, while they may also carry pressurized fluids, are usually not designed to handle the same level of internal pressure that pressure vessels are.
Shape and Structure:
Pressure vessels are often cylindrical, spherical, or conical. They are designed for structural integrity and the ability to withstand external or internal forces from all directions. In contrast, pipes are typically tubular, with a primary function of providing a conduit for fluid flow. The cylindrical shape of a pipe is optimized for fluid flow efficiency, not for withstanding internal pressure in a confined space like a pressure vessel.
Safety Features:
Pressure vessels are equipped with several safety features. These include pressure relief valves, rupture discs, and thick walls to manage high pressure safely. While pipes may have valves and fittings to control flow, they are generally not equipped with the same extensive safety measures as pressure vessels. The design of pipes is not necessarily focused on containment under high pressure, but rather on facilitating the flow of fluids.
Standards and Regulations:
Pressure vessels are regulated by strict standards, such as the ASME Boiler and Pressure Vessel Code (BPVC) or the ASME B31.3 for piping systems, which include requirements for wall thickness, material selection, and safety features. Pipes, while also governed by certain standards (such as ASME B31.3 for pressure piping), are not subject to the same level of scrutiny when it comes to pressure containment. Pipes are designed to transport fluids under moderate pressure, not to contain high pressure.
Design Intent:
The design of a pipe focuses on strength for fluid flow and leakage prevention. In contrast, the design of a pressure vessel emphasizes structural integrity to withstand high internal pressure. A pressure vessel is often a sealed, static container with internal pressure, while a pipe is a conduit designed for continuous fluid movement and pressure regulation.
Testing and Inspection:
Pressure vessels undergo rigorous testing, including pressure tests and non-destructive tests (NDT) to ensure they can safely withstand internal pressure. Pipes are tested for strength and leak resistance. However, pressure vessel testing is more stringent due to the higher risks of pressurized storage.
The Importance of Proper Classification
Proper classification of pipes and pressure vessels is vital for safety, efficiency, and regulatory compliance. Misclassifying them can lead to serious consequences.
Regulatory Compliance:
Pressure vessels face stricter safety standards than pipes, requiring specific codes (e.g., ASME BPVC) for design and inspection. Misclassification can result in legal and safety risks.
Design Accuracy:
Correct classification ensures appropriate design. Over-designing pipes or under-designing pressure vessels increases costs and safety hazards.
Cost Efficiency:
Proper classification ensures cost-effective material and design choices. Misclassification can lead to unnecessary expenses and inefficiencies.
System Reliability:
Properly classified components are better suited for their operating conditions, improving the reliability and performance of the system.
Maintenance and Inspections:
Pressure vessels require more frequent and rigorous inspections, while pipes need simpler checks. Misclassification can lead to insufficient maintenance.
Risk Management:
Correct classification supports accurate risk assessments. Misclassification can jeopardize safety protocols and lead to unforeseen failures.
Need a Reliable Partner?
Although both pipes and pressure vessels involve handling pressurized fluids, their design purposes are different, and they must be properly classified to ensure safety, efficiency, and regulatory compliance. Misclassification can lead to safety risks and additional costs. If you have any questions about pressure vessels, please feel free to contact MINNUO, and we will provide free consulting services.