The rapid population increase and human society’s modernization result in energy shortages and environmental pollution in elevated form . In recent scenarios, energy demand mainly depends on non-renewable resources globally. Continuous utilization of fossil fuels leads to a shortage of environmental issues . This thought-provoking issue opens a new area of research for exploring sustainable and clean energy. Compared to other renewable energy resources, hydrogen is considered clean energy with a high calorific value and density; it could be an ideal substitute for fossil fuels . Hydrogen production has become more critical than ever. But what are the Methods of Hydrogen Production?
Currently, the mainstream methods of hydrogen production primarily include thermochemical processes, electrolysis, direct solar water splitting, and biological processes.
In the following, this article will explore the four main methods of hydrogen production and analyze the unique aspects of each.
I. Biological Processes: Hydrogen Energy Produced by Microbial Metabolism
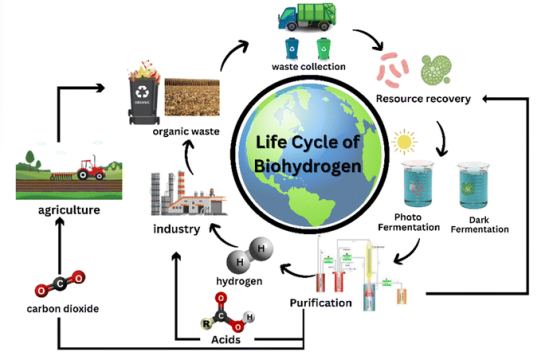
Current Status and Challenges of Biological Hydrogen Production
Biological hydrogen production primarily utilizes microorganisms such as photosynthetic bacteria and fermentative bacteria to convert organic substrates into hydrogen gas under specific conditions. At present, the hydrogen production efficiency of biological methods is relatively low, and the process is highly sensitive to environmental factors, leading to poor stability. For example, in the case of hydrogen production by photosynthetic bacteria, small fluctuations in factors such as light intensity, temperature, pH value, and substrate concentration can cause a significant decrease in the hydrogen production rate.
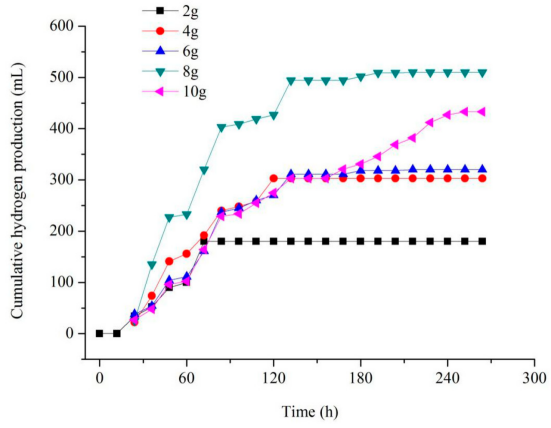
Biological hydrogen production opens up a new perspective on hydrogen generation through the unique metabolic capabilities of microorganisms. In the hydrogen production field, solar energy, as a clean energy source, offers its own unique mechanisms for water splitting. Let’s explore this together.
II. Direct Solar Water Splitting Process: Hydrogen Release Triggered by Light Energy
Diverse Attempts in Solar Hydrogen Production
Direct solar water splitting for hydrogen production mainly involves two technological routes: photocatalytic water splitting and photoelectrochemical water splitting. Photocatalytic water splitting typically uses semiconductor photocatalysts like TiO₂ and ZnO. Under sunlight exposure, these materials generate electron-hole pairs that drive the oxidation-reduction reactions in water. Photoelectrochemical water splitting, on the other hand, involves assembling a photoanode and photocathode into a photoelectrochemical cell, where photo-generated charge carriers enable the splitting of water.
Beyond simple flat-panel photocatalytic reactors, more advanced systems have been developed, combining parabolic concentrators, Fresnel lenses, and specialized reactors to enhance the efficiency of solar energy-driven water splitting.
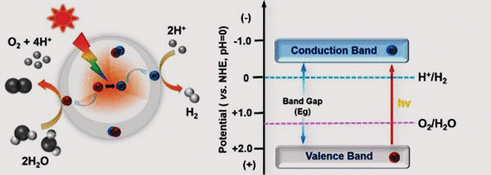
Solar hydrogen production presents an innovative path utilizing natural energy. Among the many hydrogen production technologies, thermochemical processes and electrolysis are equally important. In these processes, reactors play a vital role in significantly improving hydrogen production efficiency and supporting the industrialization of hydrogen energy. Let’s now take a deeper look at the thermochemical process.
III. Thermochemical Processes: The Transformation of Hydrogen Energy Under High Temperature and Pressure
(A) Diverse Thermochemical Hydrogen Production Methods
Thermochemical hydrogen production is typically carried out at high temperatures (>700°C) and high pressures (10–50 bar), involving complex reactions. Common equipment includes fluidized bed reactors and fixed bed reactors. The former uses gas flow to fluidize solid particles, improving heat and mass transfer efficiency, making it suitable for large-scale continuous production, such as hydrogen production through biomass gasification. The latter has a simple structure, making catalyst replacement easier and is suitable for processes under milder conditions, like steam methane reforming (SMR) for hydrogen production.
(B) Advantages of Reactors in Key Reactions
In the mainstream steam methane reforming (SMR) thermochemical hydrogen production process, the reactor plays a significant role. The SMR reaction is strongly endothermic, with the main reaction being CH₄ + H₂O ⇌ CO + 3H₂, accompanied by the water-gas shift reaction CO + H₂O ⇌ CO₂ + H₂.
- Stable Environment: The reactor body is mainly made of nickel-based high-temperature alloys, such as Inconel and Hastelloy. These materials can withstand internal pressures of up to 50 bar. Through multi-layer ceramic fiber insulation and high-efficiency heating systems, the internal temperature is stabilized in the ideal range of 800–950°C. This ensures efficient reactions and high hydrogen yield.
- Precise Control for Efficiency: Advanced reactors are equipped with high-precision temperature and pressure sensors. They also feature an automated control system based on PLC, which adjusts the heating power and gas flow rate in real-time. This ensures that the temperature and pressure remain within minimal fluctuation ranges.
- 4oThis precise control boosts the hydrogen generation rate and selectivity, thus enhancing hydrogen production efficiency.
Among the many reactor manufacturers, Minnuo stands out in the thermochemical hydrogen production field due to its technical expertise and innovation. Their reactors use nickel-based high-temperature alloys capable of withstanding 50 bar pressure, and with multi-layer ceramic fiber and in-house heating systems, they maintain temperatures between 800 and 950°C, ensuring high hydrogen yield. By utilizing high-precision sensors and an in-house PLC control system, they improve hydrogen production efficiency. Minnuo also applies CVD technology to prepare coatings that enhance corrosion resistance and reduce costs, thus solidifying the foundation for thermochemical hydrogen production.
Thermochemical processes convert chemical energy into hydrogen energy at high temperatures and pressures. The next section explores the electrolytic process, which generates hydrogen by utilizing electrical energy. In this process, reactors also play a critical role in providing strong support for efficient hydrogen production.
IV. Electrolytic Process: Hydrogen-Oxygen Separation Driven by Electrical Energy
A) Common Electrolysis Methods for Hydrogen Production
Electrolysis of water for hydrogen production is primarily divided into two technological routes based on the type of electrolyte: Proton Exchange Membrane (PEM) electrolyzers and Alkaline Electrolyzers. PEM electrolyzers use perfluorosulfonic acid proton exchange membranes as the electrolyte. They offer advantages such as high current density, high gas purity, and fast startup.This makes them particularly suitable for decentralized hydrogen production. In such scenarios, renewable energy generation is unstable, and quick response is required. Alkaline electrolyzers, on the other hand, have a more mature technology and are relatively low-cost, holding a significant market share in large-scale centralized hydrogen production.
(B) Reactors in Creating an Ideal Electrolytic Environment
Reactors serve as the supporting and protective unit for electrolysis cells, providing a stable, sealed environment for the electrolytic reaction.
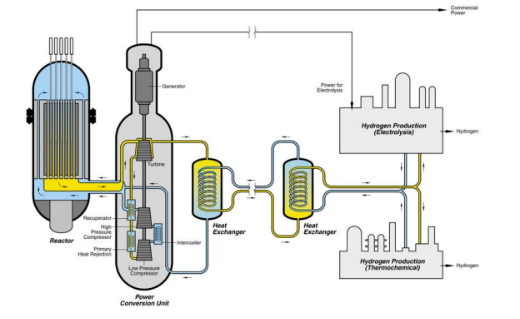
- Structural Optimization for Enhanced Reaction: The use of three-dimensional porous electrode structures and specially designed electrolyte inlet and outlet distribution systems effectively reduces local overpotentials on the electrode surface. Compared to ordinary reactors, this design significantly improves electrolysis efficiency.
- Thermal Control for Energy Savings and Performance: The thermodynamic efficiency of water electrolysis is closely related to temperature. Reactors are equipped with high-efficiency heat exchange systems, such as plate heat exchangers or spiral tube heat exchangers. Minnuo uses high-efficiency plate heat exchangers that can precisely control the electrolyte temperature within the optimal reaction range, effectively reducing electrolysis energy consumption.
- Corrosion Resistance for Stability: For electrolysis cells using alkaline electrolytes (such as 30%-35% by weight KOH solution), reactors are typically made of nickel-based alloys or titanium alloys. Surface passivation treatment or application of corrosion-resistant coatings (e.g., ruthenium oxide coating) is used to enhance their corrosion resistance. Based on these considerations, Minnuo selects high-quality nickel-based alloys for their reactors and applies advanced surface passivation treatment, ensuring stable operation over the long term.
Conclusion
At the crossroads of the energy transition, the four methods of hydrogen production will define our future. Each offers immense potential, bringing us closer to a zero-carbon world. Now is the time to embrace these technologies and move together toward a cleaner, more sustainable tomorrow!
If you have any questions about hydrogen production methods or are looking for a suitable hydrogen production reactor, feel free to contact us at MINNUO. We will provide you with free consultation!