With the continuous enhancement of global environmental awareness, wastewater treatment has become a crucial part in industrial production. Especially under strict environmental regulations, the standards for wastewater discharge are getting more and more stringent, and industrial enterprises are facing even more severe environmental challenges. During the wastewater treatment process, the selection of the coating for wastewater reactors has an extremely critical impact on the entire wastewater treatment process. Because it is not only related to the compliance of enterprises but also directly affects the effectiveness of environmental protection. As the amount of wastewater discharge increases, how to improve the treatment efficiency and reduce the negative impact on the environment by optimizing the coating of wastewater reactors has become an urgent problem that various industries need to solve.
During the wastewater treatment process, the reactor plays a vital role. As one of the core equipment, the reactor is mainly responsible for the degradation, decomposition, and transformation of harmful substances in wastewater. Its operating effect not only determines the efficiency of wastewater treatment but also has an important impact on the long-term stability and safety of the equipment. Therefore, it is crucial to choose suitable reactor equipment and coating materials. Especially when facing different types of wastewater and treatment requirements, the selection of coating for Wastewater Reactors become even more critical.
This article will conduct an in-depth technical analysis of the advantages and disadvantages of different coating materials to help enterprises make scientific and reasonable decisions.
Common Coating Types for Wastewater Reactors
The coating design of wastewater reactors is a key factor in ensuring the long-term and efficient operation of the equipment. Based on the characteristics and treatment requirements of different wastewater, common coating types include stainless steel lining, polytetrafluoroethylene (PTFE) lining, rubber lining, and ceramic coating. Each coating material has different advantages and application ranges. And choosing the right coating can effectively improve the wastewater treatment efficiency and reduce equipment wear.
Stainless steel lining:
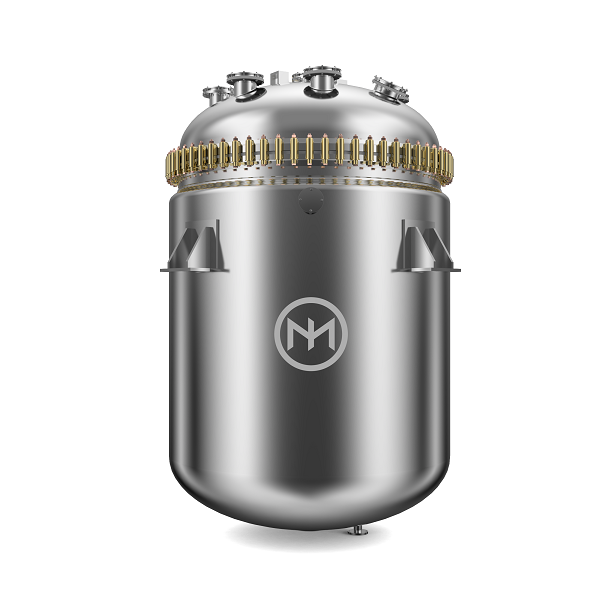
Stainless steel is widely used in industrial reactors due to its excellent strength, corrosion resistance, and high-temperature resistance. For most neutral or slightly acidic and alkaline wastewater, the stainless steel lining is an economical and reliable choice. It can withstand certain chemical erosion and shows good stability under higher temperatures and pressures. However, for strongly acidic or alkaline wastewater, a single stainless steel lining may not provide enough protection.
Polytetrafluoroethylene (PTFE) lining:
Polytetrafluoroethylene is suitable for treating strongly acidic, strongly alkaline, and solvent-based wastewater because of its outstanding chemical stability and corrosion resistance. The PTFE material hardly reacts with any chemical substances, so it can provide excellent protection when facing complex wastewater components. Its main drawback is that it is relatively expensive and has poorer high-temperature resistance compared with other lining materials.
Rubber lining:
Rubber lining is suitable for neutral wastewater or weakly acidic and alkaline wastewater. Because of its good elasticity and wear resistance, it can effectively prevent the mechanical wear of the equipment at room temperature. However, for high-temperature or highly corrosive wastewater, the rubber lining may not meet the requirements for long-term use.
Ceramic coating:
Ceramic coating is usually used to treat wastewater containing high concentrations of harmful substances, such as highly acidic or organic solvent wastewater, due to its extremely high corrosion resistance, high-temperature resistance, and hardness. The ceramic coating can effectively prevent the chemical erosion of the reactor by wastewater, but it is rather brittle and is prone to damage in an environment with large impacts or pressure fluctuations.
Best Decision Framework
How to Develop a Coating for Wastewater Reactors Selection Plan Based on Wastewater Types
The selection of the coating for a wastewater reactor needs to be comprehensively considered according to the specific chemical properties, temperature, pressure, and treatment requirements of the wastewater. Different types of wastewater require different coating materials to ensure the performance of the reactor and the long-term reliability of the equipment. Here are some coating selection suggestions for several typical wastewater types:
Oily wastewater: Oily wastewater usually has relatively low corrosiveness, but there may be high viscosity and temperature fluctuations. In this case, a polytetrafluoroethylene (PTFE) lining is a suitable choice. It can effectively prevent the pollution of the equipment by grease and reduce the fouling problem of the reactor. For oily wastewater with a relatively high temperature, a stainless steel lining can also be selected to enhance the mechanical strength.
Acidic wastewater: Acidic wastewater will have a strong corrosive effect on the inner wall of the reactor. At this time, a polytetrafluoroethylene (PTFE) lining is the best choice. Especially in the treatment of high-concentration acidic wastewater, its excellent corrosion resistance can effectively protect the equipment. At the same time, a glass-lined lining can also be selected to improve the tolerance to acidic substances.
Organic solvent wastewater: Organic solvent wastewater has a relatively strong corrosive effect on the equipment material, especially when the solvent concentration is high. To ensure the long-term operation of the reactor, choosing a PTFE lining or a ceramic coating can provide the best chemical protection. The ceramic coating can not only resist the erosion of strong solvents but also improve the heat resistance of the reactor. It is suitable for high-temperature solvent wastewater.
How to Reasonably Select a Suitable Wastewater Reactor Based on Working Temperature, Pressure, and Flow Rate
Selection of Working Temperature
When a wastewater reactor operates at different temperatures, the requirements for the high-temperature resistance, thermal expansion, and thermal stability of the materials are different. So, it is especially important to select suitable reactor materials and lining materials.
Temperature Range:
If the wastewater temperature is relatively high (such as exceeding 100℃), high-temperature-resistant materials should be selected, like a stainless steel or polytetrafluoroethylene (PTFE) coated reactor.
For a wastewater reactor operating at low or normal temperature, a common stainless steel lining or rubber lining is usually sufficient. But the aging and embrittlement of certain materials (such as rubber) caused by low temperature need to be considered.
The Influence of Temperature on Lining Materials:
Stainless steel lining: Suitable for most temperature conditions, especially for high-temperature, corrosion-resistant acidic or oily wastewater. Common materials are like 304 and 316L stainless steel.
PTFE: It has excellent high-temperature and corrosion resistance performance, but it cannot be exposed to an environment exceeding 260℃ for a long time.
Rubber lining: Suitable for normal or medium-temperature environments, but high temperature will lead to the aging and damage of rubber.
Ceramic coating: Suitable for corrosion resistance requirements at high temperature, applicable to acidic and high-temperature wastewater.
Selection of Working Pressure
The design pressure of a wastewater reactor decides its capacity to bear external pressure. It also impacts the material, thickness, and lining material choice of the reactor.
Low-Pressure Environment:
For general low-pressure wastewater treatment (such as conventional wastewater treatment, chemical substance reaction), the design pressure of the reactor is low. Ordinary carbon steel or stainless steel materials can be selected.
In a low-pressure environment, lining materials such as rubber or PTFE are suitable for treating corrosive wastewater and will not be subject to excessive mechanical pressure.
High-Pressure Environment:
For wastewater reactions that need to withstand higher pressure (such as high-pressure wastewater treatment, organic solvent reaction), the structure and material of the reactor must be of higher strength. At this time, a stainless steel reactor is more common, especially 316L stainless steel with strong pressure resistance.
In a high-pressure environment, the sealing performance and safety design of the reactor are especially important. Pressure-resistant sealing materials such as polyurethane sealing rings should be selected to avoid leakage or explosion risks.
Selection of Flow Rate
The wastewater flow rate is an important factor in determining the reactor design. It directly affects the size, structure, stirring ability, and reaction efficiency of the reactor.
Low Flow Rate:
For small-flow wastewater treatment, a smaller reactor can be selected, which helps save equipment costs. At this time, a simple type of stirring device can be selected for the reactor, and the fluid dynamic requirements are relatively low.
Small-flow reactors are suitable for laboratory-level or small-scale treatment projects. Usually, lower-cost materials (such as stainless steel lining or rubber lining) are sufficient.
High Flow Rate:
For high-flow wastewater treatment, the reactor must be able to withstand a larger liquid flow velocity and maintain a good mixing effect during the treatment process. This requires the reactor design to meet fluid mechanics requirements. The material should have wear resistance and corrosion resistance.
High-flow reactors usually need a stronger stirring system to ensure the uniform mixing of wastewater. At the same time, a larger reactor volume is required. Thick-walled stainless steel or highly wear-resistant lining materials such as PTFE or ceramic coating may need to be selected.
Maintenance and Life Cycle Management
In different wastewater treatment scenarios, managers should formulate detailed maintenance plans according to the characteristics of the wastewater, treatment requirements, and the specific usage environment of the equipment. The maintenance plan includes not only regular inspections but also the monitoring of equipment usage, data analysis, and equipment upgrades when necessary. Here are the specific maintenance methods for different wastewater types:
Maintenance of Ceramic Coating in Organic Wastewater Treatment
Ceramic coating is widely used in reactors for treating wastewater containing organic solvents or corrosive organic substances due to its excellent corrosion resistance and high-temperature resistance. However, ceramic coating is relatively fragile and prone to cracks or wear under severe temperature changes, pressure fluctuations, or mechanical impacts. So, effective maintenance measures are crucial.
Regularly inspect the ceramic coating:
It is recommended to conduct a comprehensive inspection every 3 – 6 months, especially when there are large temperature fluctuations. The inspection includes checking whether there are signs of cracks, peeling, or wear on the coating surface.
Check the operating conditions of the reactor:
Ensure that the temperature, pressure, and flow rate of the wastewater are within the design range of the reactor and avoid high pressure or temperature that may damage the ceramic coating.
Crack monitoring and repair:
Once cracks or coating damage are found, immediately stop using the reactor and carry out repairs. The repair work can be completed by coating repair techniques (such as ceramic paint supplementation). For severe damage, a complete replacement of the ceramic coating may be required.
Use professional cleaners:
Regularly use mild cleaners to clean the surface of the ceramic coating and avoid using strong corrosive cleaners or mechanical wiping that may damage the coating.
Maintenance of Polytetrafluoroethylene (PTFE) Lining in Acidic Wastewater Treatment
PTFE lining is widely used in treating acidic wastewater due to its excellent acid resistance. To ensure its long-term corrosion resistance and efficiency, regular maintenance work is also crucial.
Regularly check the integrity of the lining:
Inspect the surface of the PTFE lining every 6 months and confirm whether there is corrosion, wear, or deformation. Especially in areas that have more severe contact with acidic wastewater, such as inlets, outlets, and reaction zones.
Monitor the pH value and temperature of the wastewater:
Ensure that the pH value of the wastewater matches the design requirements of the reactor and avoid a too strong acidic environment that may affect the PTFE lining. At the same time, monitor the temperature of the wastewater and avoid high temperature that may cause aging or deformation of the PTFE material.
Regularly replace seals and lining joints:
Due to long-term chemical corrosion, the sealing performance of the PTFE lining may decline. Regularly check and replace the sealing parts and the lining material at the joints to ensure the sealing of the equipment.
Maintenance of Stainless Steel Lining in Oily Wastewater Treatment
Stainless steel lining is usually used in treating oily wastewater. Its maintenance is relatively simple, but regular inspections are also needed to avoid corrosion and wear after long-term use.
Regularly check for signs of corrosion:
Inspect the stainless steel lining every 6 – 12 months. Focus on checking whether there are microcracks, corrosion, or rust at the welds. Especially when the wastewater contains high grease or chemical substances, the stainless steel lining may have local corrosion.
Clean grease accumulation:
When treating oily wastewater, the stainless steel lining is prone to grease accumulation. Regularly use a special solvent to clean and ensure that the surface of the lining is not affected by grease deposition and improve the reaction efficiency.
Avoid excessive temperature and pressure:
Although stainless steel has high heat resistance and strength, long-term use under temperature and pressure conditions beyond its design range may lead to a decline in material performance. So, ensure that the operation is within the recommended temperature and pressure range.
Maintenance of Rubber Lining
Rubber lining is often used in treating neutral or mildly corrosive wastewater. Since rubber material has good elasticity and wear resistance, but it is prone to aging and cracking under high temperature, strong corrosion, or long-term use. So, regular maintenance is crucial to ensure the long-term operation of the equipment.
Check surface wear and cracks:
Inspect the rubber lining every 6 months. Pay special attention to areas with more friction, such as inlets, outlets, reaction zones, etc., and check whether there are signs of wear, cracks, or aging.
Avoid high temperature and strong corrosive substances:
Try to avoid exposing the rubber lining to high temperature and strong corrosive substances. For wastewater with higher temperature or stronger corrosiveness, consider using a more heat-resistant and corrosion-resistant lining material.
Regularly apply protective oil:
To prevent the aging and cracking of rubber material, an appropriate rubber protective oil can be applied to the surface to help extend its service life.
Conclusion and Recommendations – Minnuo Offers Customized Solutions for You
In the selection of coatings for wastewater reactors, the most crucial decision-making factors are the chemical properties of the wastewater, the operating environment, and the working characteristics of the equipment. Choosing the right coating can not only effectively improve the wastewater treatment efficiency but also extend the service life of the equipment and reduce maintenance costs. It is vital to select the most suitable coating materials by comprehensively considering factors such as temperature, pressure, and flow rate, and combining specific wastewater types (such as acidic, alkaline, or oily wastewater) with operating conditions.
Minnuo, relying on its rich industry experience, can provide customers with customized coating solutions for wastewater reactors. Our professional team will design the optimal plan according to customer needs to ensure the efficient operation of the equipment. Welcome to contact us. We will provide you with comprehensive technical support and high-quality product delivery.