Recently, with the increasing production demands for highly corrosive, extreme temperature, and high-pressure environments, companies have become more reliant on glass-lined equipment. Especially for glass-lined reactors, due to their excellent corrosion resistance and high-temperature performance, they have become an ideal choice for many companies to solve production challenges. However, when choosing a glass-lined reactor, many people face a key question: “Is the enamel layer of glass-lined equipment thicker always better?” This seemingly simple question hides complex technical considerations and decision-making traps.
The choice of enamel layer thickness is not simply about “the thicker, the better.” While a thicker enamel layer can provide stronger corrosion resistance and a longer service life, it also brings higher costs, increased weight, and potential reductions in thermal conductivity efficiency. Therefore, the thickness of the enamel layer must be chosen based on factors like the corrosiveness of the materials being processed, the temperature and pressure of the working environment, and the frequency of equipment use.
Next, we will uncover the technical secrets behind choosing the enamel layer thickness. This will help you make more cost-effective procurement decisions while ensuring efficient and stable operation of the equipment.
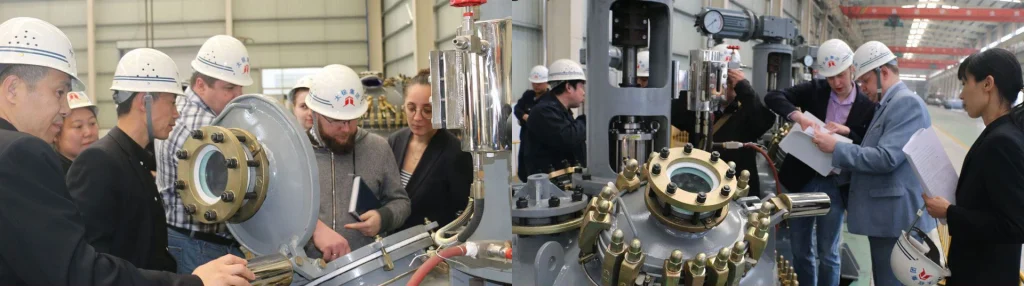
The Role and Importance of the Enamel Layer
One of the key advantages of glass-lined equipment is its enamel layer. As the interface between the equipment and the reactants, the enamel layer not only gives the equipment corrosion resistance, high-temperature resistance, and impact resistance, but also determines the equipment’s durability and reliability. Understanding the basic functions and durability of the enamel layer is crucial when selecting a glass-lined reactor.
Corrosion Resistance
Acid and Alkali Resistance: The enamel layer effectively prevents the corrosion of strong acids, alkalis, and other aggressive chemicals, ensuring the long-term stable operation of the reactor in chemical environments.
Solvent Resistance: The enamel layer resists corrosion from organic solvents, preventing solvents from penetrating the inner walls of the equipment, especially in industries like pharmaceuticals.
Salt Resistance: The enamel layer prevents the corrosion of salt substances, ensuring the reactor’s stability in salty environments.
High-Temperature Resistance
High-Temperature Stability: The enamel layer can withstand temperatures above 600°C, ensuring the equipment remains stable in high-temperature environments.
Thermal Expansion Performance: The enamel layer has a thermal expansion coefficient close to that of the metal substrate, preventing cracks or delamination due to temperature changes.
Mechanical Strength
Impact Resistance: The enamel layer has high impact resistance, allowing the equipment to withstand external shocks during operation.
Scratch Resistance: The enamel layer is resistant to friction and scratches, effectively extending the equipment’s service life.
The Impact of Enamel Layer Thickness on Equipment Performance
Thin Enamel Layer
- Advantages: Lower cost, suitable for low-corrosion and low-temperature environments.
- Disadvantages: Poor corrosion resistance, easily damaged in high-temperature, high-impact, or highly corrosive environments.
Thick Enamel Layer
- Advantages: Excellent corrosion resistance, extends the equipment’s lifespan, suitable for high-corrosion and high-temperature environments.
- Disadvantages: Higher cost, increased weight, may affect heat conduction efficiency.
Factors Affecting the Selection of Enamel Layer Thickness
Properties of the Reaction Materials
- Corrosiveness: The stronger the corrosive nature of the chemicals, the thicker the enamel layer needs to be to provide stronger protection. For example, in environments with strong acids, alkalis, or solvents, a thicker enamel layer effectively prevents equipment corrosion.
- Temperature: In high-temperature environments, the enamel layer needs to be thicker to ensure the equipment’s stability and long-term durability. High temperatures may cause thin enamel layers to deform or damage, so increasing thickness enhances heat resistance.
Operating Environment of the Equipment
- Pressure: In high-pressure environments, the enamel layer thickness must be increased to enhance the reactor’s mechanical strength and pressure resistance, preventing damage under pressure.
- Reaction Time and Frequency: For reactors used frequently or for long periods, the enamel layer is prone to wear. Increasing thickness appropriately can extend its lifespan and reduce issues caused by wear.
Economic Considerations
- Cost and Budget: When the budget is limited, an appropriate enamel layer thickness can be chosen to balance the equipment’s functionality and initial investment costs.
- Long-Term Operating Costs: Although a thicker enamel layer increases initial investment, its improved durability significantly reduces maintenance and replacement costs. In the long run, it offers better economic benefits.
How to Choose the Right Enamel Layer Thickness
Choosing the right enamel layer thickness is key to ensuring the performance and long-term stable operation of the enamel-lined reactors. Here are a few important tips to help you select the right thickness while controlling costs and maximizing investment returns.
Choose Based on Industry Standards
Different industries have different requirements for enamel-lined equipment. You can refer to industry standards and equipment specifications to choose the right enamel thickness. For example, in industries like pharmaceuticals and chemicals, the corrosiveness and temperature conditions of the reaction materials vary, so the enamel layer thickness requirements differ as well. Following industry standards ensures that the equipment meets the specified safety and performance requirements.
Our Enamel-Lined Reactors—The Perfect Thickness
When you choose our enamel-lined reactors, you will receive a tailored solution with the enamel layer thickness just right for your needs. We combine professional design with your process requirements to provide the most suitable enamel thickness. Our Minnuo reactors offer durability while optimizing production and maintenance costs, helping you achieve a higher return on investment.
Balance Cost and Performance
Our enamel-lined reactors not only meet high performance standards but also focus on cost control. When selecting the right enamel thickness, we ensure that the equipment runs stably over the long term while reducing both initial investment and future maintenance costs, helping you achieve the best investment return.
Conclusion:
Choosing the right enamel layer thickness is key to ensuring the performance and durability of the enamel-lined reactor. By considering the nature of the reaction materials, operating environment, and economic factors, the right enamel thickness can improve corrosion resistance, high-temperature resistance, and mechanical strength, while extending the equipment’s lifespan and lowering maintenance costs. Our enamel-lined reactors are customized based on industry standards and client needs to ensure the optimal enamel thickness, helping you achieve efficient, safe, and economical production. Choose us for professional solutions and the best investment return.