Recently, there has been an increasing focus on healthcare, especially after the pandemic, which has made us more aware of the crucial role the pharmaceutical industry plays in safeguarding health. From life-saving vaccines to medications for various diseases, pharmaceutical manufacturing is not only related to the safety of each individual’s life but also to our everyday health. While drugs and vaccines are the final products, the complex production processes behind them rely on precise, efficient, and safe equipment support, and among these, pressure vessels are key to ensuring that these processes run smoothly.
Pressure vessels are essential in the pharmaceutical industry, serving as the backbone for a range of key manufacturing processes. Whether it’s chemical synthesis, sterilization, or biopharmaceutical fermentation, these vessels create the high-pressure environments necessary for reactions, sterilization, and storage of volatile substances. Their ability to precisely control temperature, pressure, and other critical parameters ensures that pharmaceutical products are manufactured safely, consistently, and at the highest quality standards.
In this article, we’ll delve into the specific roles of pressure vessels in pharmaceutical production, the industry standards they must meet, and how they contribute to the scalability and safety of drug manufacturing.
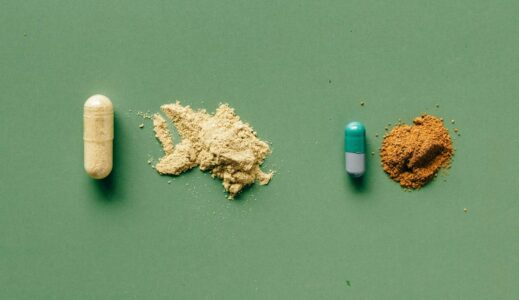
What is the Pharmaceutical Manufacturing Industry?
The pharmaceutical manufacturing industry is responsible for the production of medications and vaccines used to treat a wide range of medical conditions. This industry plays a vital role in healthcare, ensuring the availability of both generic and branded medicines that are crucial for improving and saving lives.
How Are Pressure Vessels Used in Manufacturing Medicines?
Pressure vessels are critical equipment in pharmaceutical manufacturing, used primarily for reactions, sterilization, and storage processes. These vessels are designed to withstand high-pressure conditions, enabling complex processes essential for pharmaceutical production. Next, let’s explore some key applications of pressure vessels in pharmaceutical manufacturing.
A. Reaction Vessels for Chemical Synthesis
synthesis processes. These vessels are equipped to handle the pressure and temperature conditions required to initiate chemical reactions. This is crucial in drug formulation and production. Certain medications require chemical reactions under controlled pressure to form active pharmaceutical ingredients (APIs), intermediates, and other compounds.
Key Roles:
- Catalysis: Some pharmaceutical processes require catalysts that work more efficiently at elevated pressures.
- Solvent Control: Pressure vessels allow for the proper mixing of solvents, chemicals, and reactants under specific pressure conditions that promote optimal yields.
- Closed Systems: To prevent contamination, pressure vessels maintain a closed environment during synthesis, ensuring that the final product is free from external impurities.
B. Sterilization and Pasteurization
Pressure vessels are commonly used for sterilization and pasteurization in pharmaceutical manufacturing. Some medications, especially biological products like vaccines or insulin, require heat treatment to eliminate harmful microorganisms without compromising efficacy. This process often uses autoclaves, specialized pressure vessels that provide steam or dry heat at high pressures and temperatures.
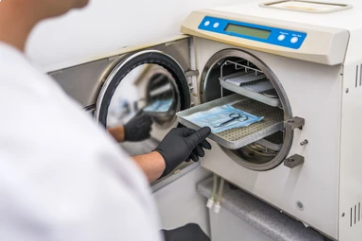
- Sterilization: In this process, steam is injected into a pressure vessel to achieve the necessary temperature and pressure to sterilize equipment, containers, and even the final product.
- Pasteurization: Similar to sterilization, pasteurization involves exposing pharmaceutical liquids (such as vaccines or serums) to controlled heat in a pressure vessel to kill bacteria and other pathogens, while preserving the integrity of the product.
C. Storage and Containment of Volatile Substances
Pharmaceutical manufacturing often involves storing volatile chemicals or gases that must be contained under pressure for safety and efficiency. Pressure vessels are designed to safely store gases and liquids essential for production, which may be hazardous under normal conditions. For example, reactive gases used in pharmaceutical ingredient synthesis are stored in pressurized tanks to prevent escape or maintain the desired pressure for chemical reactions.
Applications:
- Nitrogen and Oxygen Storage: In pharmaceutical manufacturing, pressurized nitrogen and oxygen may be used for both sterilization and creating inert atmospheres during reactions.
- CO₂: Carbon dioxide in pressurized vessels may be used in supercritical fluid extraction, a technique for extracting active ingredients from raw plant materials or other substances.
D. Fermentation Systems in Biopharmaceuticals
The biopharmaceutical sector, which deals with biologics like vaccines, antibodies, and enzymes, often relies on pressure vessels in fermentation and bioreactor systems. These vessels maintain the optimal environment for growing cultures of bacteria, yeast, or mammalian cells. These cultures produce therapeutic proteins or vaccines.
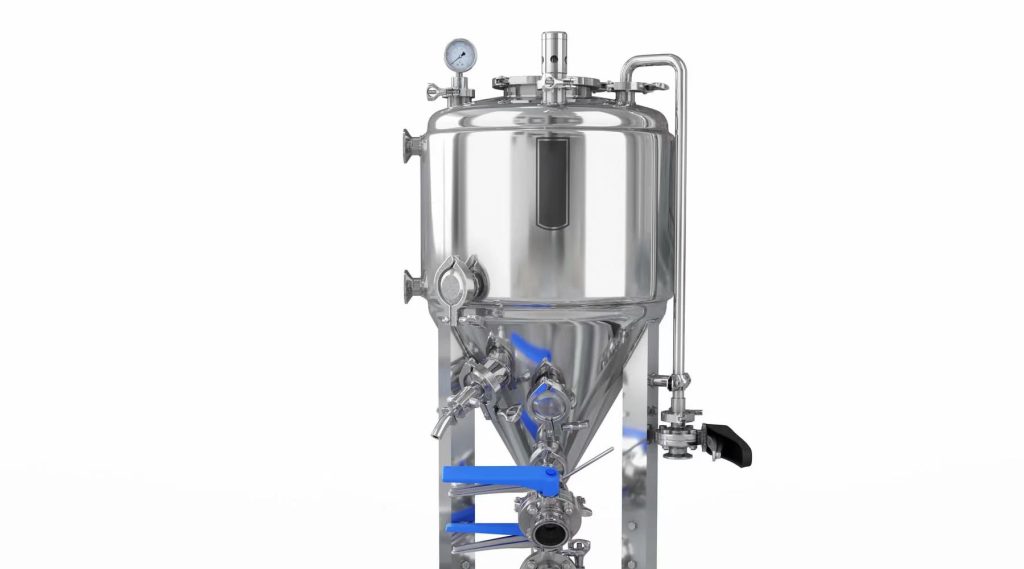
Key Roles:
- Bioreactors: These pressure vessels are used to provide precise control over oxygen levels, temperature, and pressure to cultivate microbial cultures or cell lines in large-scale production.
- Fermentation: During fermentation, pressure is often applied to promote the growth of microorganisms that generate valuable pharmaceuticals.
What are the Standards for Pressure Vessels in Pharmaceutical Manufacturing?
Pressure vessels used in pharmaceutical manufacturing must adhere to stringent industry standards to ensure both safety and product quality. Regulatory bodies such as the U.S. Food and Drug Administration (FDA), European Medicines Agency (EMA), and International Society for Pharmaceutical Engineering (ISPE) set specific guidelines for designing, maintaining, and inspecting these vessels.
- Good Manufacturing Practice (GMP): The FDA’s GMP guidelines are essential in ensuring that pharmaceutical pressure vessels maintain high levels of hygiene and safety throughout the manufacturing process. This includes protocols for cleanliness, sterilization, and maintaining pressure integrity.
- ASME Standards: The American Society of Mechanical Engineers (ASME) issues standards such as ASME Section VIII for the design, fabrication, and inspection of pressure vessels. These standards are critical to ensuring that pharmaceutical vessels operate safely under high-pressure conditions.
Why Are Pressure Vessels Essential for Pharmaceutical Manufacturing?
Pressure vessels are essential in pharmaceutical manufacturing for several reasons:
- Precision Control: They provide the necessary control over temperature, pressure, and time, ensuring that pharmaceutical processes meet the required specifications for high-quality production.
- Safety: Pressure vessels are designed with multiple safety features, such as pressure relief valves, to prevent accidents and equipment failures.
- Efficiency: By creating controlled environments, pressure vessels increase process efficiency, reducing the time required to produce pharmaceutical products while ensuring the desired outcome.
Related Questions People Ask About Pressure Vessels in Pharmaceutical Manufacturing
A. What types of pressure vessels are used in pharmaceutical manufacturing?
In pharmaceutical manufacturing, the most common types of pressure vessels are reactors, autoclaves, and bioreactors. Each serves a different purpose, from chemical synthesis to sterilization and fermentation.
B. How are pressure vessels maintained in pharmaceutical manufacturing?
Regular maintenance is essential for ensuring the safe operation of pressure vessels. This includes routine inspections, cleaning to prevent contamination, pressure testing, and calibration of safety mechanisms like pressure relief valves.
C. How do pressure vessels affect the scalability of pharmaceutical production?
Pressure vessels are crucial for scaling pharmaceutical processes from laboratory to commercial production. Their ability to maintain consistent conditions under varying volumes of raw materials and outputs makes them ideal for large-scale production.
Conclusion
Pressure vessels are indispensable in the pharmaceutical manufacturing industry. They play a critical role in processes ranging from chemical synthesis to biopharmaceutical production.These vessels ensure that the pharmaceutical products meet the stringent requirements for safety, quality, and efficacy.As the pharmaceutical industry evolves, the demand for innovative pressure vessel technologies will grow. Compliance with regulatory standards will be crucial to ensuring the production of safe and effective medicines for global health needs.
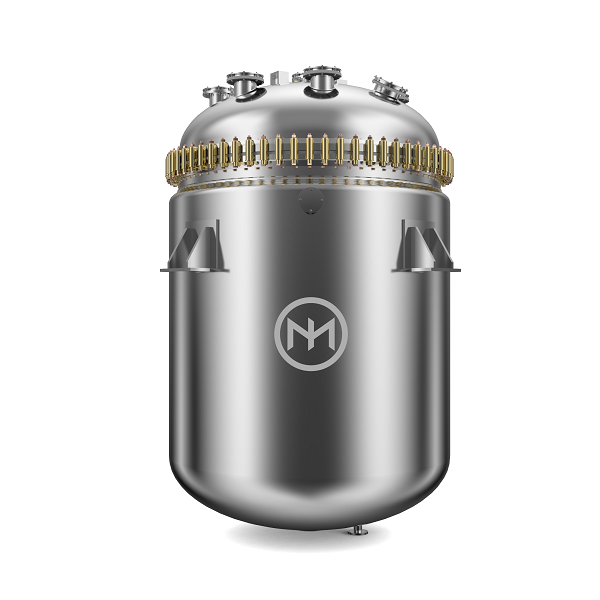
As a professional pressure vessel solutions provider, we understand the high standards the pharmaceutical industry requires for equipment. Whether it’s chemical synthesis, sterilization, or biopharmaceuticals, MINNUO provide a complete set of systematic technical support. This ensures you stay ahead in the highly competitive market.