A one-stop solution supplier for reaction Kettle Systems
- Free solution design
- Automation control systems
- On-site installation and inspection
Reaction Automation control System
We provide comprehensive customized solutions
Reaction automation control system includes reactor body, stirring device, heating and cooling system, control module, filtration device, nitrogen purge system, tail gas collection system, etc. It ensures that the equipment realizes the process of heating, cooling or evaporation through data monitoring and plc automation control function. You can keep abreast of the project process, monitor the status of the equipment, the real-time data of the instrumentation and the chemical reaction status, and it is applicable to many industries such as chemical, petroleum and pharmaceutical, mineral, medical, food, and so on.
- Imprve Project Efficiency
- Enhance Stability
- Adaptable to Multiple Scenarios
- Reduce Operational Risks
our reactor types
Glass-lined Reactor
Enameled glass reactors are widely used in industries such as chemical, pharmaceutical, and food processing, especially suitable for chemical reactions involving highly corrosive substances like acids and alkalis. Made with materials resistant to corrosion and high temperatures, they ensure product purity and reaction safety, maintaining the stability of the reaction process.
- Inner Vessel Design Pressure: -0.1 to 1.6 MPa
- Temperature range inside the vessel: -19°C to 200°C
- Jacket Design Pressure: 0 to 4 MPa
- Jacket temperature range: -19°C to 260°C
- Capacity Range: 20L to 50,000L
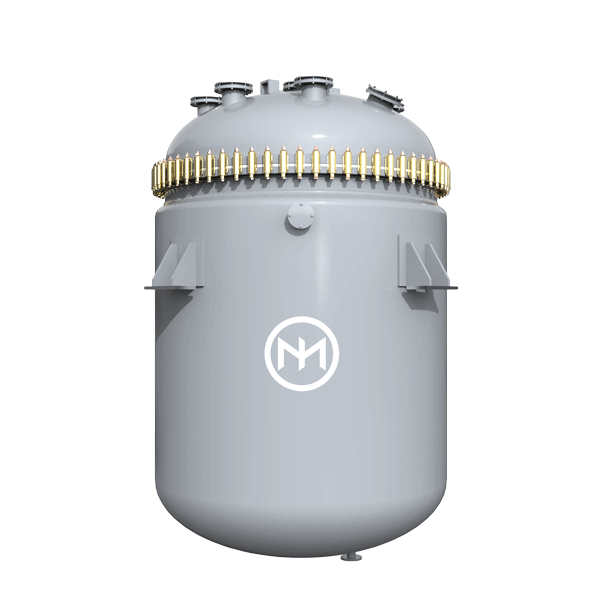
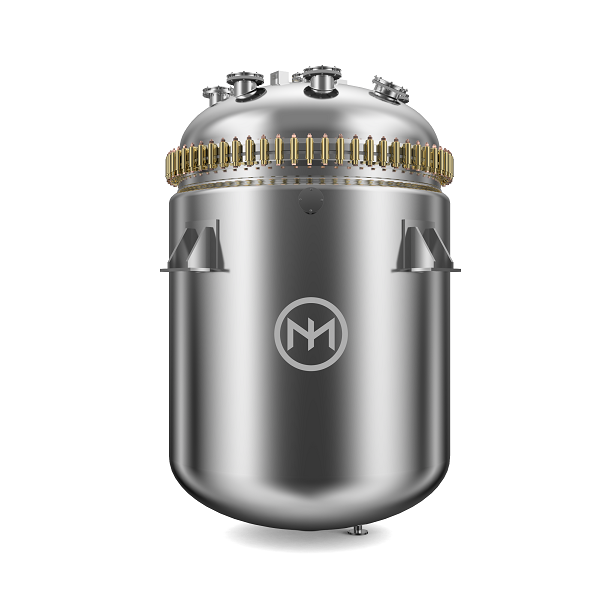
Stainless Steel Reactor
Stainless steel reactors, on the other hand, are more commonly used in industries such as petrochemical, metallurgy, and power generation, especially for reactions involving high temperatures, high pressures, and solid materials. Compared to enameled glass reactors, stainless steel reactors offer stronger mechanical strength and greater pressure resistance, making them suitable for more complex and large-scale industrial reactions.
- Nominal capacity:50~5000L
- Jacket capacity:95~1400L
- Motor power: 1450/0.6~1450/7.5
Working Principle of the Reaction Kettle
The required raw materials are added to the reactor in a specific proportion. The materials are typically introduced through the feeding port, and the reactor is designed with good sealing to prevent leakage of substances during the reaction process.
The reactor is heated by a heating device (such as electric heating, steam heating, or jacket heating) to reach the required reaction temperature. The temperature control system continuously monitors and adjusts the temperature to ensure that the reaction takes place at the optimal temperature.
The reactor is equipped with a stirring device (such as paddle, anchor, or screw type), which continuously mixes the reaction materials, ensuring uniform distribution of components and enhancing the reaction rate and efficiency.
Under the combined effects of temperature, pressure, and stirring, the materials undergo a chemical reaction to produce the desired products. Depending on the reaction type, this may be accompanied by the release of gases, heat changes, and other phenomena.
After the reaction is completed, the reactor uses a cooling system (such as a cooling jacket or condenser) to lower the temperature inside the reactor, ensuring the stability of the product. The waste gases and liquids generated during the reaction can be discharged through an exhaust system.
How to Choose Between Stainless Steel and Enamel-Lined Reactors ?
- better heat transfer efficiency
- withstand higher pressures
- easy to clean
- More cost-effective
- Corrosion resistance
Criteria | Stainless Steel Reactors | Enamel Reactors |
---|---|---|
Corrosion Resistance | √ Slightly less effective in strong acid/alkali environments | √ Excellent in strong acid environments |
Heat Transfer | √ Faster heat transfer, higher efficiency | √ Slower heat transfer |
Cost | √ Higher initial cost, low maintenance, long lifespan | √ Lower cost, ideal for tight budgets |
Pressure Resistance | √ Suitable for high-pressure environments | Poor pressure resistance, risk of enamel cracking |
Hygiene | √ Smooth surface, easy to clean | Enamel layer may have micropores, less hygienic |
Customization | √ Highly flexible and customizable | Limited customization options |
Reactor System Specialists
We specialize in custom reactor systems, delivering efficiency, reliability, and safety tailored to your industry's needs.
Multifuctional and High Efficiency Reaction Kettle Solutions and Advantages
Reactors, also known as reaction vessels, are specialized containers designed to facilitate chemical reactions under controlled conditions. They are more than just steel tanks—they represent a blend of engineering expertise and material science.

Multi-functional High-Integration Design

Diverse Structures and Configurations

Customized Solutions and Complete Systems

On-Time Delivery

Professional After-Sales Support

Technological Innovation
Reaction Vessel Application Cases
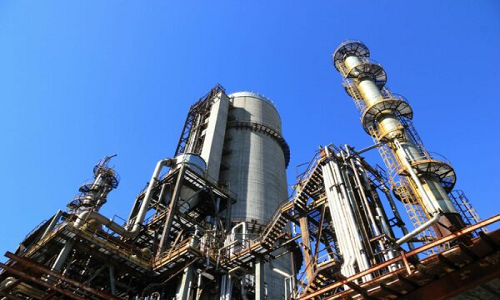
Industrial Chemical Reactor
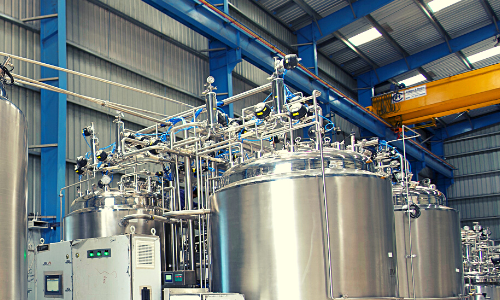
Reactors In Pharma Industry
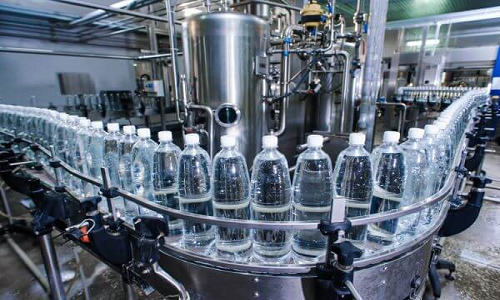
Food and Beverage Industry
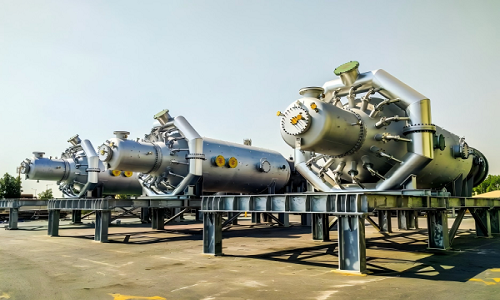
Petrochemical Industry
Factory Showcase
Jiangsu Minnuo Group Co., Ltd. was established in 1987 with a registered capital of 120 million RMB. It is a pioneer in the field of reactors and related solutions. With advanced automated production lines and internationally leading technology, our factory possesses efficient and precise production capabilities, capable of meeting the needs of high-end clients. Our strict quality control system covers every production process, ensuring that each reactor has excellent corrosion resistance and high-temperature performance. The technology R&D center within the factory continuously drives innovation, providing customers with cutting-edge solutions.
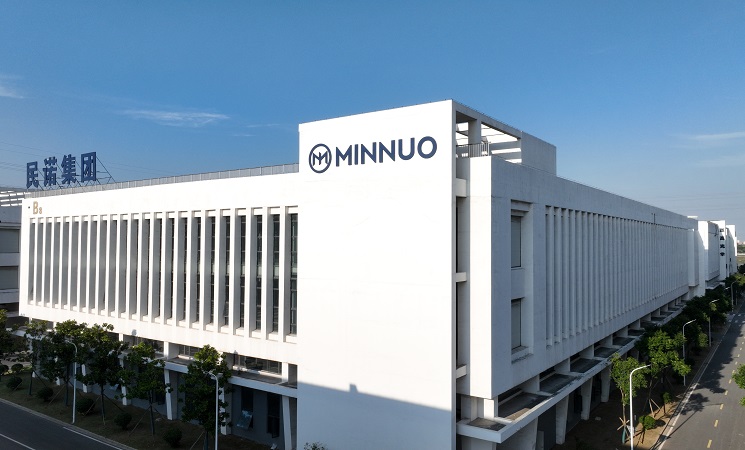
Related Products
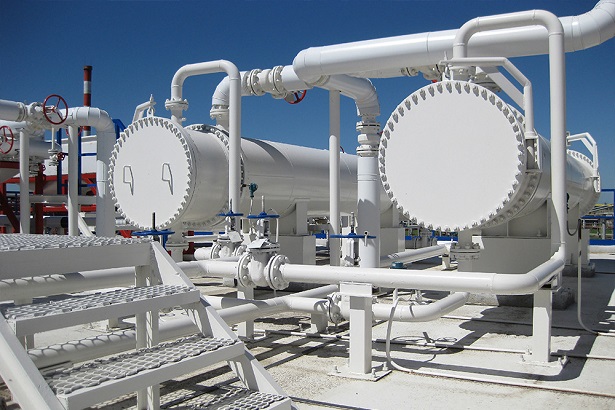
Heat Exchanger
Compact, lightweight, excellent heat transfer performance, high pressure and temperature resistance, easy installation, and low maintenance.
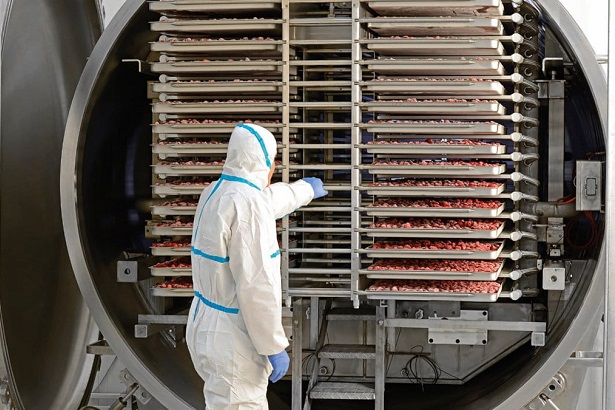
Dryer
Compact design, stable operation, fast dehumidification, and automated control.
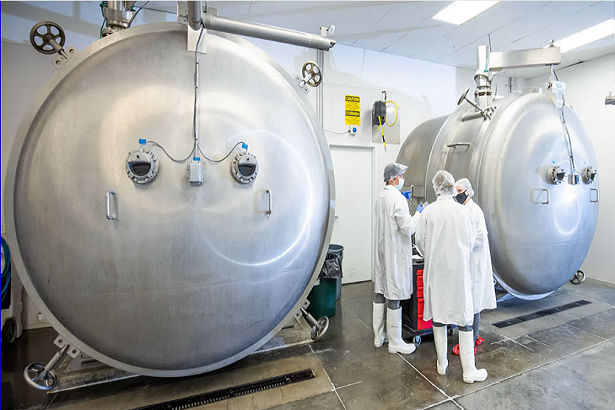
Evaporator
High pressure resistance, excellent anti-frost performance, and adaptability to various operating conditions.
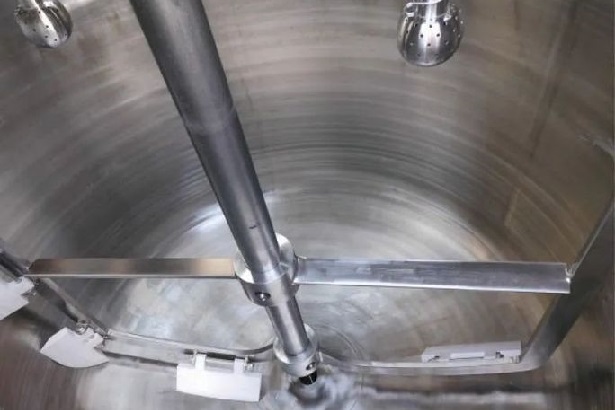
Agitator
Made from high-temperature and corrosion-resistant materials, providing uniform mixing and suitable for demanding conditions.
How to Confirm the Solution ?
- 1.Confirm the Materials: Materials can be gaseous, liquid, solid, or mixed (If some components of the material are confidential and cannot be provided, please confirm the material requirements).
- 2.Confirm the Reaction Temperature.
- 3.Confirm the Reaction Pressure.
After confirming the above important parameters, you can fill out the side form and contact our professional technicians to give you a comprehensive quotation and solution!
We offer specialized reactor solutions
“*” is a required field