Amid the global wave of transitioning to clean energy, CNG (compressed natural gas) is gaining significant attention as a low-carbon and eco-friendly energy source. Its applications are expanding rapidly across industries, including the automotive sector, public transportation, and industrial gas storage. As the core component of CNG systems, cylinder performance and selection play a crucial role in ensuring energy safety and efficiency. In this context, the differences in cylinder materials have become a hot topic in the industry. Steel cylinders are renowned for their durability, while composite cylinders are increasingly favored for their lightweight design and high performance. So, what are the differences between steel cylinders and composite cylinders? How should you choose between them in practical applications?
The contrast between steel and composite cylinders is quite striking. Steel cylinders excel with their high strength and cost-effectiveness, making them ideal for industrial gas stations and standard vehicles. However, their heavier weight and lower resistance to corrosion can pose challenges in scenarios requiring lightweight solutions or exposure to corrosive environments. On the other hand, composite cylinders stand out with their lightweight structure, corrosion resistance, and exceptional burst performance, making them the preferred choice for premium vehicles, marine environments, and cold climates. Although they come with higher costs and more complex maintenance, they significantly enhance energy efficiency and meet the demands of specialized applications. The material differences directly influence factors such as weight, strength, durability, and cost, resulting in distinct suitability for various scenarios.
Next, we will delve into the manufacturing processes of these two types of cylinders and analyze their unique strengths in terms of performance, applications, and future trends.
Steel Cylinders: Traditional Advantages and Robust Durability
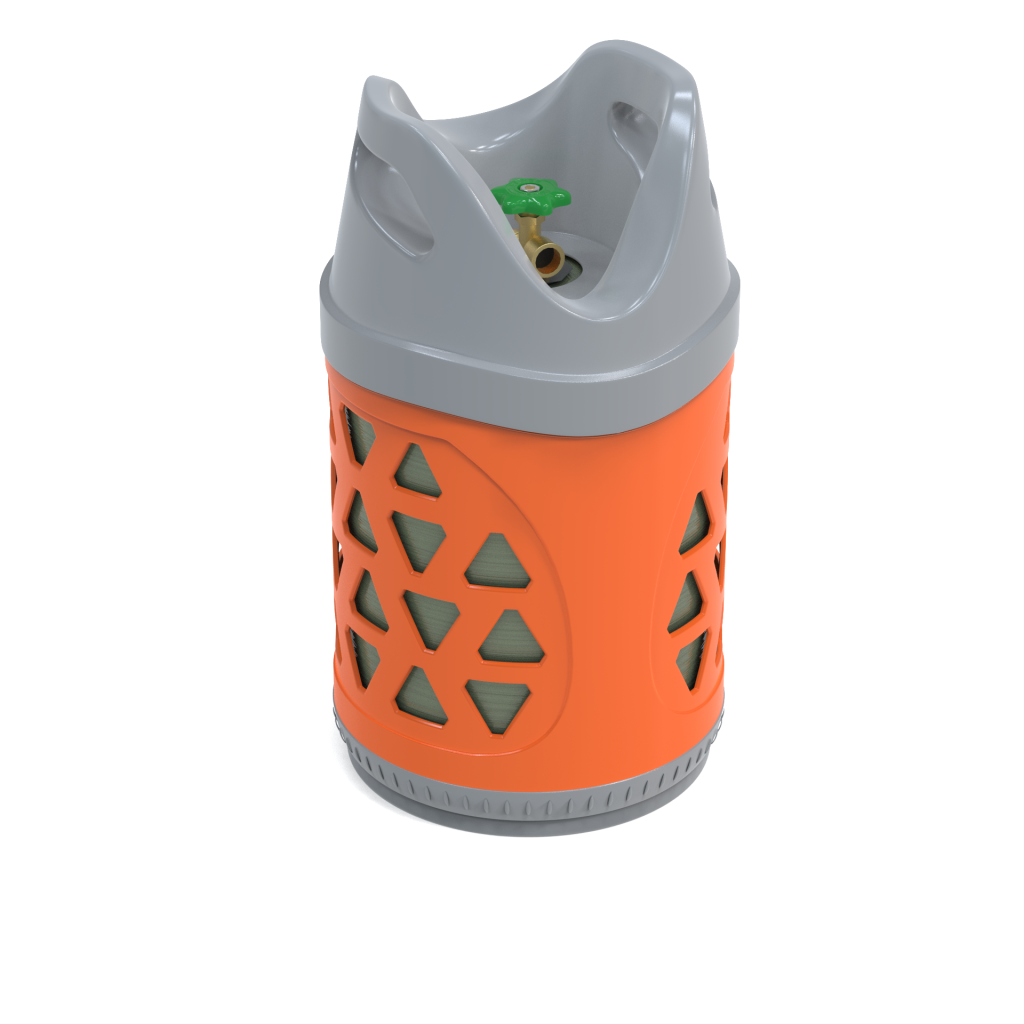
Steel cylinders are the earliest type of CNG cylinders, made from high-strength steel and often featuring a seamless structure.
Key Features:
- High Strength: Steel cylinders offer excellent pressure resistance, making them suitable for most CNG storage applications.
- Strong Durability: The material resists wear and tear, performing well in heavy-use and harsh environments.
- Cost-Effective: Compared to composite cylinders, steel cylinders have lower manufacturing costs and are more competitively priced.
Main Drawbacks:
- Heavy Weight: Steel cylinders are relatively heavy, which increases the overall load of vehicles and reduces fuel efficiency.
- Corrosion Risk: In humid or corrosive environments, steel cylinders may face corrosion issues, requiring regular maintenance.
Composite Cylinders: The Blend of Lightweight Design and High Performance
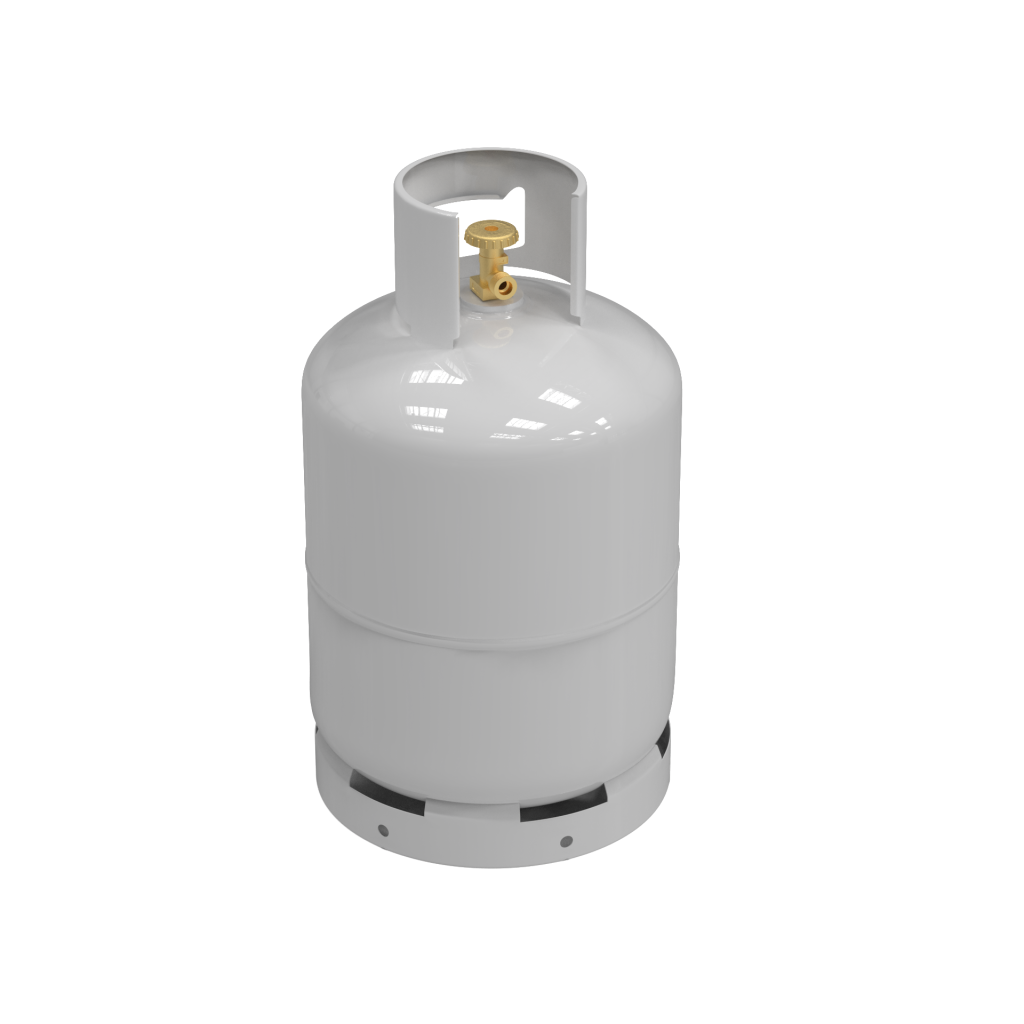
Composite cylinders use materials like carbon fiber, glass fiber, or other composites, often combined with a metal or plastic liner.
Key Features:
- Lightweight Design: Composite cylinders are 30%-70% lighter than steel cylinders, which significantly reduces vehicle load and improves fuel efficiency.
- Strong Corrosion Resistance: Composite materials resist corrosion effectively, making them suitable for long-term use.
- High Safety Standards: Composite materials offer excellent burst resistance, ensuring stability under high-pressure conditions.
Main Drawbacks:
- Higher Costs: The complex manufacturing process and expensive materials make composite cylinders more costly than steel cylinders.
- Challenging Maintenance: Inspecting and repairing composite cylinders is more difficult, and they require stricter usage conditions.
Performance Comparison Summary: Steel Cylinders vs. Composite Cylinders
Performance Metric | Steel Cylinders | Composite Cylinders |
Weight | Heavier | Lighter, reducing vehicle load |
Strength | High | High, with additional burst resistance |
Corrosion Resistance | Lower, requiring regular protection | High, suitable for corrosive environments |
Cost | Lower | Higher |
Maintenance | Simple | More complex |
Applications | Industrial and standard vehicles | Premium vehicles and public transport |
Application Scenarios for Different Types of Cylinders
Steel and composite cylinders serve distinct purposes in various fields, and their material characteristics determine their performance in specific applications.
Application Scenarios for Steel Cylinders
Steel cylinders, known for their high strength and cost-effectiveness, are primarily used in the following areas:
- Industrial Gas Storage Stations: Steel cylinders offer excellent pressure resistance and durability, making them ideal for stationary storage systems, such as those found in factories.
- High-Pressure Industrial Applications: For tasks like welding and cutting, which require stable high-pressure output, steel cylinders provide superior impact resistance.
- Fuel Systems for Standard Vehicles: In commercial trucks or budget-friendly cars, where weight is less of a concern, steel cylinders are widely used due to their cost advantage.
Application Scenarios for Composite Cylinders
Composite cylinders, valued for their lightweight design and high performance, are better suited for the following uses:
- Automotive and Public Transport: For long-distance transportation and public vehicles like buses, reducing weight is critical. Composite cylinders help improve fuel efficiency and range.
- Marine Environments: Composite materials resist corrosion in high-salinity conditions, making them ideal for offshore platforms and marine gas storage systems.
- Cold Regions: Composite cylinders maintain stable performance in extreme low temperatures and are resistant to brittleness, making them perfect for gas storage in cold climates.
- Portable Gas Equipment: Due to their light weight and ease of transport, composite cylinders are commonly used in portable gas devices or personal gas storage systems.
In-Depth Discussion on Application Scenarios
Do composite cylinders offer better advantages than steel cylinders in marine environments?
Marine environments feature high salt content and high humidity, which can cause steel cylinders to corrode easily. Even with surface protection, their lifespan may still be limited. Composite cylinders, on the other hand, have excellent corrosion resistance due to their material properties. They perform better during prolonged exposure to marine conditions. For example, on offshore oil and gas platforms, composite cylinders provide more stable performance and help reduce maintenance costs.
Are composite cylinders more suitable for use in cold regions? Why?
In cold environments, steel cylinders can become brittle due to extremely low temperatures, which affects their safety. Composite cylinders, however, have a low thermal expansion coefficient and maintain stable performance in very low temperatures. This makes them ideal for gas transportation and storage in cold regions. For instance, in natural gas transportation across the Arctic, composite cylinders prove to be safer and more reliable.
Can lightweight composite cylinders fully replace steel cylinders? Where are the limitations?
Although composite cylinders are gradually replacing steel cylinders due to their lightweight design and high performance, they are not suitable for every scenario:
- Cost Limitations: The manufacturing cost of composite cylinders is high, so steel cylinders remain a more economical option for budget-sensitive applications.
- High-Pressure Industrial Equipment: In situations that require extremely high strength and impact resistance, such as industrial welding or high-pressure cutting, steel cylinders perform better.
Therefore, in applications where weight is not a priority or where cost is a major concern, steel cylinders continue to be the mainstream choice.
Does cylinder material still matter for hybrid or electric vehicles?
Even in hybrid or electric vehicles, the choice of cylinder material remains very important. Many new energy vehicles have strict requirements for energy efficiency and range. The lightweight advantage of composite cylinders helps reduce overall vehicle weight and improves energy utilization. Moreover, with increasingly strict environmental regulations, the low carbon footprint of composite materials is also a significant benefit.
Will industrial stationary gas storage equipment adopt composite materials?
As composite material technology continues to evolve, its use in industrial stationary gas storage equipment is becoming more feasible. Although steel cylinders still dominate due to their cost-effectiveness and reliability, composite cylinders are showing potential in specific scenarios. In high-corrosion environments or portable industrial storage units requiring lightweight solutions, composite cylinders are emerging as a viable option. For example, in mobile storage units within large industrial parks, composite cylinders are now being explored as a new direction.
Differences in Manufacturing Processes and the Impact of Material Choices for Steel and Composite Cylinders
By analyzing manufacturing processes, material properties, and practical application scenarios, we can better understand the strengths and weaknesses of steel and composite cylinders. While composite cylinders are becoming a mainstream trend due to their lightweight design and high performance, steel cylinders remain important in specific markets because of their durability and cost-effectiveness.
What are the key differences in the manufacturing processes of steel and composite cylinders?
The manufacturing process for steel cylinders mainly uses high-strength steel. Steel undergoes hot rolling or cold rolling to form seamless tubes, followed by heat treatment and high-pressure testing. This well-established process is suitable for large-scale, standardized production, ensuring high strength and excellent sealing performance.
In contrast, composite cylinders involve more complex processes. The liners are typically made from metal or plastic materials, with an outer layer reinforced using fiber winding techniques. The fibers used include carbon fiber and glass fiber. During production, additional steps such as resin curing, pressure testing, and fatigue resistance evaluation ensure the combination of lightweight design and high strength.
These process differences directly influence the performance characteristics of the cylinders, particularly in terms of weight, strength, and cost. Furthermore, material selection plays a crucial role in shaping these outcomes.
Differences Between Carbon Fiber and Glass Fiber in Composite Cylinders: Which Performs Better?
In composite cylinders, carbon fiber and glass fiber are the most common materials used for external reinforcement. Each offers unique strengths and weaknesses in terms of strength, weight, and cost:
- Carbon Fiber: This material provides higher strength and stiffness while being lighter, making it ideal for applications that prioritize weight reduction, such as in automotive and aerospace fields. However, it comes with higher manufacturing costs, making it more expensive.
- Glass Fiber: Although slightly less strong than carbon fiber, glass fiber meets the needs of most applications and is significantly more affordable. It is well-suited for projects where cost-effectiveness is a priority.
Overall, carbon fiber offers superior performance, but glass fiber remains widely used due to its cost advantages. Different material choices can also affect the fatigue performance of cylinders, a key metric for assessing quality.
How Is Fatigue Strength of Cylinder Materials Evaluated?
Fatigue strength refers to a cylinder’s ability to withstand repeated pressure cycles without failure. There are several methods to evaluate the fatigue performance of cylinder materials:
- Pressure Cycle Testing: This test simulates the pressure changes during gas filling and release to check for cracks or deformation in the material.
- Static Load Testing: This method applies sustained stress under high pressure to observe the fatigue failure point of the material.
- Finite Element Analysis (FEA): Digital simulation tools predict material performance under complex stress conditions.
Does the Liner Material of Cylinders Affect Insulation Performance?
The liner material of a cylinder impacts not only structural stability but also insulation performance. Common liner materials include:
- Metal (e.g., Aluminum Alloy): Metals have high thermal conductivity, making them suitable for scenarios with rapid pressure changes. However, their insulation performance is relatively low.
- Plastic (e.g., HDPE): Plastics offer excellent insulation and are lightweight, but they may deform under high temperatures, requiring additional protective measures.
Composite cylinders typically use plastic liners for better insulation, while steel cylinders rely on external coatings or layers to enhance insulation since the steel itself conducts electricity. The choice of liner material must balance thermal conductivity and insulation based on specific application needs.
How Do Cylinder Materials Affect Pressure Release Speed?
The strength and ductility of cylinder materials directly influence the stability of pressure release:
- Steel Cylinders: Their high rigidity ensures stable pressure release under normal conditions. However, in sudden pressure release scenarios, such as ruptures, the reaction can be more intense.
- Composite Cylinders: The outer fiber layers have some ductility, which helps distribute stress during pressure release and reduces the risk of sudden rupture. This characteristic makes composite cylinders considered safer.
Conclusion
By comparing the material properties, manufacturing processes, and application scenarios of steel and composite cylinders, it is clear that both have unique advantages for specific needs. Steel cylinders, with their high strength and low cost, perform well in industrial gas storage stations and standard vehicles. On the other hand, composite cylinders, known for their lightweight design, corrosion resistance, and high safety, are the ideal choice for premium vehicles, marine environments, and cold regions.
In addition, composite cylinders excel in fatigue strength and pressure release safety, while steel cylinders remain indispensable in high-pressure industrial equipment and cost-sensitive applications.
If you have any questions about the performance or other aspects of steel and composite cylinders, feel free to visit our Minnuo website and connect directly with our technical team. We are always ready to provide you with more detailed answers. Additionally, we offer a variety of steel and composite cylinders to suit different scenarios. Whether you prioritize performance or cost-effectiveness, we are here to provide the best solutions for your needs!