With the continuous development of industrialization, the use of pressure vessels has become increasingly widespread in various fields, especially in industries such as chemicals, pharmaceuticals, and food, where they play a crucial role. However, despite the progress in modern technology, the safety of pressure vessels still faces challenges. Pressure vessel welding types directly impact the overall structure and safety of the container. Any defects could lead to catastrophic consequences, even risking lives.
Choosing the right welding types of pressure vessel is critical. Common welding methods include Shielded Metal Arc Welding (SMAW), Flux-Cored Arc Welding (FCAW), Gas Metal Arc Welding (GMAW), Tungsten Inert Gas (TIG) welding, and Submerged Arc Welding (SAW). Among these, TIG welding is the preferred choice for manufacturing high-strength, pressure-resistant pressure vessels due to its high precision, excellent fusion, and weld quality. Compared to other methods, TIG welding offers significant advantages in ensuring sealing, reducing welding defects, and enhancing pressure resistance.
Next, we will explore the types of welding used in pressure vessels and the advantages of TIG welding in pressure vessel manufacturing, explaining why it has become the industry’s top choice.
Welding Quality and Pressure Vessel Safety: Case Study Analysis
In the design and manufacturing of pressure vessels, welding quality is one of the key factors determining the safety of the vessel. Poor welding practices or improper maintenance can lead to vessel failure, even catastrophic accidents. Although many people consider pressure vessel explosions to be a problem left over from the early stages of industrialization, this risk still exists and occasionally occurs in modern industrial settings.
A notable example occurred in 2019 at a chemical plant in Texas, USA, where an explosion was caused by a welding defect in a pressure vessel. The incident happened at a plant producing petrochemical products, where a pressure vessel developed a crack after prolonged high-pressure operation, leading to vessel rupture and a violent explosion. Investigations revealed that the accident was directly linked to the welding quality of the pressure vessel. The welding process of the vessel did not strictly follow international standards, and there were small defects in the welds. These defects gradually expanded during long-term high-pressure operation, ultimately leading to the catastrophic outcome.
This event once again highlights the importance of high-quality welding processes in ensuring the safety of pressure vessels, especially in operations involving high-pressure chemical reactions, hazardous chemicals, or precise industrial processes. It is essential to ensure that the welding process meets strict industry standards and safety requirements.
Common Welding Types in Pressure Vessels
Shielded Metal Arc Welding (SMAW):
This welding process uses a consumable electrode coated with flux and is widely considered the classic form of arc welding. It is highly portable, with inexpensive and readily available equipment. However, the welding quality largely depends on the welder’s skill level, so experienced operators are necessary to ensure high-quality welds.
Flux-Cored Arc Welding (FCAW):
This method uses a consumable electrode with a flux core. Similar to SMAW, the welding process relies on the heat generated by the arc. However, FCAW uses a continuous wire feed, requiring less skill than SMAW, making it more suitable for welders with intermediate skills.
Gas Metal Arc Welding (GMAW):
The GMAW process uses a continuous wire feed electrode and inert gas protection, making the welding process simpler. Compared to SMAW and FCAW, it provides cleaner welds with fewer defects. However, this method can still experience fusion errors, which may affect welding quality, especially in more complex structures.
Gas Tungsten Arc Welding (GTAW/TIG):
Tungsten Inert Gas (TIG) welding is known for its high precision, cleanliness, and welding quality, making it essential in pressure vessel manufacturing. Although it is more difficult to operate and has a slower welding speed, TIG welding is the best choice when high-quality welds, pressure resistance, and sealing properties are required.
Submerged Arc Welding (SAW):
SAW is a process where the welding area is submerged in flux to avoid contamination from atmospheric oxygen and other gases. This method offers a high deposition rate and excellent welding quality, but it is not suitable for field operations. It requires bulky equipment, so it is mainly used in factories or large-scale welding projects.
Why Tungsten Inert Gas (TIG/GTAW) Welding is Chosen for Pressure Vessels
- High Welding Quality: TIG welding produces clean, smooth welds with almost no defects such as porosity, slag inclusion, or cracks. This ensures the strength and sealing of the welded areas in pressure vessels.
- Excellent Fusion and Penetration: Since the tungsten electrode is non-consumable and inert gas protection is used, TIG welding provides good fusion and deep penetration, making it suitable for high-pressure, high-strength vessel requirements.
- Precise Control: TIG welding allows precise control over current, heat input, and welding speed. It reduces the heat-affected zone, which helps maintain the mechanical properties and structural integrity of the material. This makes it especially suitable for thin-walled and high-precision pressure vessel welding.
- Suitability for High Cleanliness Requirements: TIG welding effectively avoids contamination, as no impurities are introduced during the welding process. It is ideal for applications with strict cleanliness standards, such as pressure vessels in the food, pharmaceutical, and chemical industries.
- Long-term Stability: TIG welding ensures consistent weld quality, making it reliable for pressure vessels in harsh environments, such as high pressure and temperature conditions. This guarantees the safety and reliability of pressure vessels over long-term use.
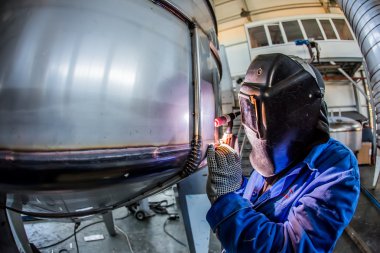
MINNUO Pressure Vessels – Ensuring Safety and Reliability with TIG Welding Technology
In the production of pressure vessels, welding quality directly impacts the safety and reliability of the product. To ensure the stable operation of equipment like glass-lined reactors under high pressure and temperature, we always use Tungsten Inert Gas (TIG) welding technology.
TIG welding can create high-strength, precise welds, ensuring the sealing of joints and preventing defects like porosity and cracks. This guarantees the pressure resistance and safety of reactors. Thanks to its excellent fusion and penetration, MINNUO pressure vessels consistently maintain superior pressure resistance and stability in harsh environments.
We understand that the safety of pressure vessels is closely related to the life and property of every user. Therefore, MINNUO commits to adhering to international standards for every pressure vessel that leaves our factory. We use top-tier TIG welding technology to ensure that your equipment remains stable, reliable, and worry-free.
Conclusion:
In today’s fast-paced industrial landscape, pressure vessel safety is critical. TIG welding technology acts as a strong safeguard for MINNUO pressure vessels, ensuring a solid safety barrier. We remain committed to international standards, expert craftsmanship, and continue to empower our products with TIG technology. Our goal is to protect the safety and well-being of every user, support the steady advancement of industries, and contribute to industrial development with peace of mind. Together, we can look forward to a safe and efficient future.