Pressure vessels are widely used in industries such as oil, gas, and chemicals, where they are responsible for safely storing high-pressure gases or liquids to ensure operational safety and stability. However, designing a reliable pressure vessel is not a straightforward task, as engineers must consider the various forces the vessel will encounter in different operating environments. Static and dynamic loads are two critical factors that influence the design and safety of pressure vessels. Understanding and properly addressing these loads are fundamental to ensuring the long-term safe operation of the vessel.
Static loads refer to constant, stable forces, such as the internal operating pressure and the weight of the vessel itself, which remain unchanged over time. In contrast, dynamic loads involve time-varying forces, such as vibrations caused by equipment, shock loads, or pressure fluctuations.
In the following sections, we will explore the key concepts of static and dynamic loads and discuss how to use this knowledge to design safer, more durable pressure vessels that can handle the challenges posed by real-world operating conditions.
What is Load? The Relationship Between Force and Load
Before delving into static and dynamic loads, it is essential to clarify the meaning of “load” in the context of pressure vessels. Load refers to the external forces or moments applied to a structure. These forces can arise from various factors, such as internal pressure, gravity, temperature changes, or external impacts. In simple terms, a load is any external force that could potentially cause deformation, damage, or operational issues in the vessel.
To understand the concept of load, it is first important to distinguish between force and load. Force is a vector quantity that describes a push or pull, typically quantified in newtons (N) or pounds-force (lbf). A load, on the other hand, refers to the total force applied to a structure or component over a given period, taking into account how these forces are distributed. Pressure vessels must be designed to withstand the total effect of these forces, whether static or dynamic.
What is Static Load?
A static load refers to a load that is applied gradually and remains constant or nearly constant over time. It does not vary with time or frequency, and its effects are predictable and stable. In pressure vessel design, static loads typically include:
- Internal Pressure: The pressure exerted by the fluids (gas, liquid, or slurry) inside the vessel. This pressure is usually uniform and constant during normal operation.
- Dead Load: The weight of the pressure vessel itself and any permanently attached components (e.g., piping, supports, insulation, etc.).
- External Load: These loads may come from structural supports, gravity, or the weight of additional equipment, and they are usually constant and predictable.
How to calculate?
When performing static load calculations, engineers rely on equilibrium equations from mechanics. The sum of all external forces acting on the pressure vessel must equal zero. Similarly, the sum of all external moments must also equal zero. Specifically, this means that both the resultant force (the vector sum of all external forces) and the resultant moment (the algebraic sum of all external moments) must be zero. This condition is the foundation of static analysis and ensures that the system is in static equilibrium without any acceleration or motion.
In pressure vessel design, the goal of static load analysis is to verify whether the vessel can maintain stability under the applied static loads without experiencing permanent deformation or material yielding. For loads caused by internal pressure, the analysis often involves calculating hoop stress, longitudinal stress, and shear stress to evaluate whether the pressure vessel can withstand the combined effects of internal and external forces.
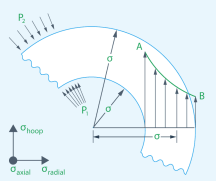
Furthermore, to ensure the vessel’s safety under normal operating conditions, static load designs often take into account a safety factor. This ensures the vessel structure has enough strength. It provides a margin to handle variations in operating conditions or operational errors.Through comprehensive calculation and analysis of all static loads, engineers can determine the vessel’s wall thickness, support strength, and material selection to guarantee its long-term stability and reliability.
What is Dynamic Load?
Unlike static loads, a dynamic load is a load that varies over time and is typically caused by moving or fluctuating forces. These loads are harder to account for in pressure vessel design. Their magnitude and direction may change, causing additional stresses or fatigue over short periods.Common types of dynamic loads include:
- Vibration: Caused by mechanical equipment or pumps connected to the pressure vessel, which can lead to oscillations or vibrations.
- Impact Load: When a sudden, intense force is applied (such as from an external collision or internal pressure changes), causing rapid stress variations.
- Pressure Fluctuations: In some systems, internal pressure may fluctuate due to changes in flow rate, temperature, or system operations (e.g., in compressors, boilers, or pipelines).
- Thermal Loads: Temperature variations can cause thermal expansion or contraction in the vessel material. When temperature changes are rapid or uneven, dynamic stresses may be generated.
Dynamic loads have a more complex effect on pressure vessels. Besides the immediate forces applied, dynamic loads often lead to fatigue, where materials weaken gradually due to repeated loading. Dynamic load analysis is essential to ensure the vessel’s durability and safety. This is especially important when the load fluctuates over time.
How to Design for Static and Dynamic Loads?
To ensure that pressure vessels can withstand both static and dynamic loads, careful planning and rigorous analysis are required during the design process. Specialized codes and standards, such as the ASME Boiler and Pressure Vessel Code (BPVC) or API 650, are often used to guide material strength calculations and determine safety factors. Below are the steps taken during the design process to address both types of loads:
1. Static Load Design
When designing a pressure vessel to handle static loads, the following steps are typically involved:
- Determine Internal Pressure: Calculate the internal pressure the pressure vessel will experience under expected operating conditions. This pressure will affect the vessel’s wall thickness, material selection, and overall strength.
- Consider Dead Load: Ensure that the weight of the vessel itself, along with any attached equipment, is included. Structural supports and foundations must be sufficiently strong to bear these static loads.
- Consider External Loads: Account for wind loads, seismic loads, or any other constant loads that the vessel may encounter based on its installation location.
The stress analysis for static loads typically uses classical methods. These include hoop stress and longitudinal stress formulas. They are commonly applied to analyze cylindrical pressure vessels.The objective is to ensure the vessel’s walls, joints, and components are strong enough. They must withstand these constant forces without failure.
The formula for calculating hoop stress (σθ) is:
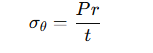
Longitudinal stress (σz) is generally smaller but should not be ignored, especially at the closure or support points of the vessel. The classical formula for calculating longitudinal stress is:
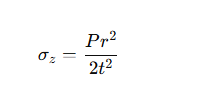
Where P is the internal working pressure, r is the vessel’s internal radius, and t is the wall thickness.
For thin-walled pressure vessels, radial stress (σ_r) is typically negligible, as when the wall thickness is much smaller than the internal radius, the radial stress has minimal impact compared to hoop and longitudinal stresses. In cases where r/t≫1, radial stress can be ignored.
2. Dynamic Load Design
Dynamic load design requires more complex approaches due to the uncertainty and variability of these loads. Key strategies for addressing dynamic loads include:
- Dynamic Load Calculation: Identify the sources of dynamic loads, such as vibrations from equipment, pressure transients, and thermal fluctuations. Simulation tools like Finite Element Analysis (FEA) can be used to model the vessel’s behavior under these varying loads.
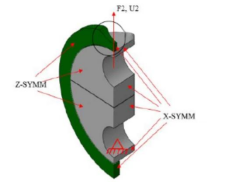
- Fatigue Analysis: Since dynamic loads often lead to fatigue, fatigue analysis is essential to determine how many load cycles the vessel can withstand before failure. This involves calculating stress ranges and applying S-N curves (stress vs. number of cycles) to assess material durability.
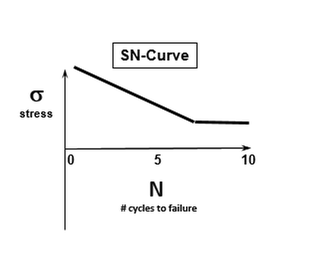
- Impact Load Protection: Considering possible impact loads, ensure that the vessel can withstand the most severe instantaneous loads, such as those from rapid valve closures or system start-up and shutdown processes.
- Damping and Vibration Control: For pressure vessels affected by persistent or fluctuating vibrations, incorporate damping devices or supporting structures into the design to mitigate the impact of dynamic loads.
Key Dynamic Loads to Consider:
- Seismic Loads: In regions prone to earthquakes, seismic loads may cause significant displacement or stress in the pressure vessel. The design should account for seismic loads and apply appropriate seismic design factors.
- Pulsating Pressure: In some systems, pressure fluctuations caused by pumps or compressors may occur. The design must ensure that the vessel can endure these pressure shocks or pulsations.
- Temperature Fluctuations: Rapid temperature changes can induce thermal stresses. Under dynamic loading conditions, the vessel must maintain integrity during expansion and contraction without cracking or deforming.
Conclusion
Through a detailed analysis of static and dynamic loads, we can see that the design of pressure vessels must not only consider the impact of constant loads but also effectively address the challenges posed by dynamic loads. A well-designed pressure vessel ensures long-term stability and safety while being capable of withstanding varying operating conditions. If you’re looking for a pressure vessel suitable for your project, or if you have any questions about the design process, feel free to contact Minno at any time. We offer free professional consultations to help you resolve all technical issues, from design to selection.