In the rapidly evolving pharmaceutical industry, ensuring the safety, efficiency, and quality of production processes is more critical than ever. With the growing global demand for high-quality pharmaceuticals, production equipment must meet the highest safety and performance standards. Among these essential devices, reactors are especially important, and stainless steel reactors have become a key choice in the pharmaceutical industry due to their versatility, durability, and compliance with regulatory standards. They play an indispensable role in the production of drugs and active pharmaceutical ingredients (APIs).
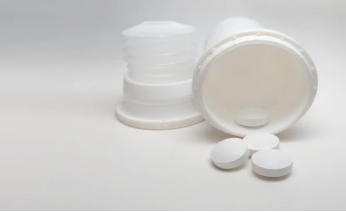
Stainless steel reactors are essential for ensuring product purity by preventing contamination, handling hazardous chemicals safely, and precisely controlling critical parameters. From ensuring product safety to meeting stringent regulatory requirements such as GMP and FDA guidelines, stainless steel reactors provide the reliability needed by pharmaceutical manufacturers. Their excellent chemical resistance, ease of maintenance, and integration with automation systems further enhance their appeal in the pharmaceutical sector.
Next, let’s explore why stainless steel reactors are the ideal choice for modern pharmaceutical production.
High Standards for Product Purity
As part of pharmaceutical manufacturing, you know that product purity is absolutely critical. Whether you’re handling active pharmaceutical ingredients (APIs) or the final drug formulation, even the smallest impurity can cause serious problems. Contamination not only affects the drug’s effectiveness but can also result in adverse side effects or harm patient health.
In this process, the choice of reactor material is especially important. If the reactor material reacts with the drug components or releases unwanted substances, contamination can easily occur. This is why stainless steel reactors are so popular in the pharmaceutical industry—it is an inert material, meaning it won’t react with the drug components. Stainless steel has a smooth surface that’s easy to clean and disinfect, helping you maintain high hygiene standards and prevent microbial growth between batches.
Therefore, if you want to ensure your products meet the highest purity standards and are safe for patients, stainless steel reactors are undoubtedly a great choice.
Meeting Strict Regulatory Standards for Compliance
Compliance is crucial in pharmaceutical manufacturing, and you should be well aware of the importance of GMP (Good Manufacturing Practices) and FDA regulations. These are not just guidelines; they are the foundation for ensuring that drugs are safe, effective, and stable. The design and material selection for reactors must adhere to these strict standards to guarantee product safety.
For example, GMP requires that all manufacturing equipment, including reactors, use safe, durable, and easy-to-clean materials. This prevents contamination and ensures that each production cycle remains consistent. Stainless steel meets all these requirements. It is non-toxic, easy to clean, and can withstand the cleaning and disinfection processes mandated by both GMP and FDA.
By choosing stainless steel reactors, you’re not just ensuring compliance; you’re also making your production process more efficient and safe.
Superior Chemical Resistance and Durability
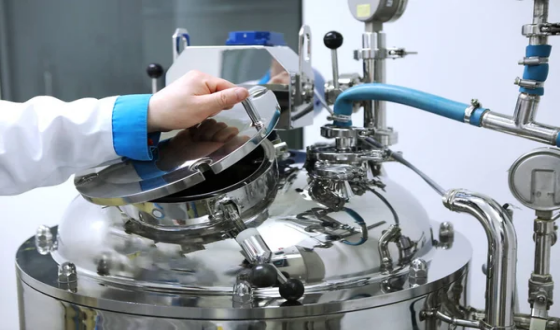
In the pharmaceutical industry, reactors are often used to handle highly reactive or corrosive chemicals. Whether it’s acids, solvents, or other compounds, you need a reactor that can withstand these materials without being damaged. Corrosion or degradation of the reactor could contaminate your product or delay production.
This is where stainless steel truly shines. It offers excellent corrosion resistance, maintaining stability even when exposed to corrosive chemicals. The surface of stainless steel forms a protective oxide layer, preventing corrosion. This ensures that the reactor won’t degrade or affect the quality of the production when dealing with these chemicals. Additionally, stainless steel can withstand high temperatures and pressures, which are essential for many reactions in pharmaceutical processes.
When you choose stainless steel, you’re opting for durability. You’re investing in a material that can perform consistently under harsh conditions, avoiding the hassle of frequent repairs or replacements.
Guaranteeing Safety and Stability in Manufacturing Processes
Safety is at the core of pharmaceutical manufacturing, and the safety of the reactor is especially important. The chemicals you’re handling can often be hazardous, and if the reactor material is unsuitable, it could lead to leaks, explosions, or uncontrolled reactions, all of which could have serious consequences.
Stainless steel reactors provide exceptional structural strength, capable of withstanding pressure and vibrations, ensuring that they won’t leak during operation. This prevents product contamination or worker exposure to dangerous substances. Furthermore, stainless steel maintains stable reaction conditions—whether temperature, pressure, or reaction speed—ensuring that chemical reactions proceed as expected and without instability. This stability reduces the risk of accidents and ensures the consistency and high quality of drug production.
When you choose stainless steel reactors, you’re not just choosing safety; you’re ensuring the stability and integrity of the entire production process.
Customization to Meet Specific Pharmaceutical Production Needs
In pharmaceutical manufacturing, the processes are often complex, and each drug production process has its own specific requirements. Each drug or active pharmaceutical ingredient (API) may require different conditions to achieve optimal reaction outcomes, making the flexibility and adaptability of reactors crucial. Stainless steel reactors are highly favored for their adaptability, as they can be customized to meet your specific needs.
Stainless steel reactors come in various sizes and designs, which can be adjusted according to the scale of your production. Whether you need small-scale research and development reactors or large-scale production reactors, stainless steel reactors can meet these diverse needs. Furthermore, reactors can be equipped with features such as agitators, heating/cooling jackets, pressure control systems, and filtration systems, tailored to meet specific process conditions. This level of customization ensures that your production process can proceed smoothly and efficiently, while also offering the flexibility to adapt to changing demands.
If your manufacturing process involves handling sensitive substances or requires precise control over temperature, pressure, or mixing, stainless steel reactors can also be equipped with advanced features to ensure that every process variable is precisely controlled.
Seamless Integration with Modern Automation Systems
Stainless steel reactors can be easily integrated with automation systems, allowing precise monitoring and control of critical parameters such as temperature, pressure, pH, and reaction time. Many stainless steel reactors are also equipped with sensors and controllers, allowing operators to view real-time data, remotely adjust settings, and ensure that the reaction conditions remain optimal at all times. This integration not only reduces the potential for human error but also increases operational efficiency, ensuring that every batch meets the required standards.
Conclusion
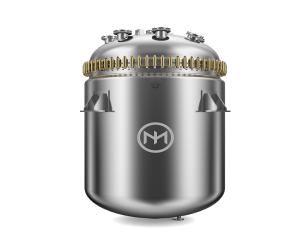
In the pharmaceutical industry, selecting the right reactor is crucial to ensure product purity, regulatory compliance, chemical resistance, and process safety. Stainless steel reactors are the optimal choice for these needs.
Our stainless steel reactors are designed for durability and reliability, equipped with features like pressure relief valves, explosion-proof systems, and automated monitoring to ensure safety and performance. With certifications like ISO 9001, ASME, and CE marking, our reactors meet the highest industry standards. These certifications guarantee our products are built to last, with uncompromised safety and quality.
By choosing Minnuo, you invest in reactors that ensure compliance, safety, and efficient production. Trust Minnuo for reliable, industry-leading solutions.